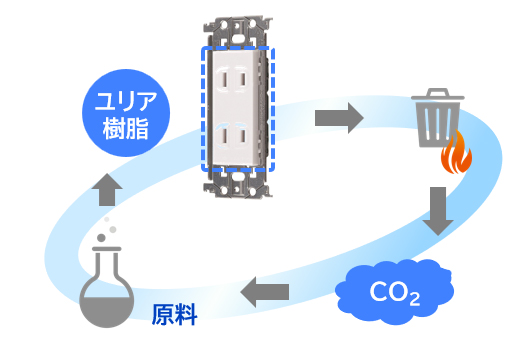
2025年4月10日
- 技術・研究開発
- プレスリリース
- 事業会社
- Panasonic GREEN IMPACT
- 環境・サステナビリティ
- 電設資材
国際的な総合科学雑誌Natureオンライン版に、記事広告「Three sustainable Japanese technologies to watch」が掲載されました。当ページの内容はNature(※1)オンライン版(2023年9月1日)に掲載された該当記事広告(※2)を日本語に翻訳したものです(日本語版文責:パナソニック ホールディングス株式会社)。
ガラス建材一体型ペロブスカイト太陽電池、グリーン水素製造技術の開発、植物由来のセルロースファイバー成形複合材料「kinari(キナリ)」について紹介されています。ぜひ、ご覧ください。
※1 Natureは世界中の読者に最先端の科学を伝える国際的な総合科学雑誌です。
※2 記事広告はNature2023年11月23日号へ掲載予定の特集企画に収載されます。
建築物の窓や壁面に用いるガラス一体型太陽電池、クリーンな水素エネルギー、植物由来のバイオプラスチックの実用化に向けた研究開発に進展が見られている。
日本政府はここ数年、「2050年までに海洋プラスチックごみによる追加的な汚染をゼロにする」「2050年までにカーボンニュートラルを実現する」など、持続可能な社会の実現に向けた宣言を出している。日本は、バイオプラスチックと水素エネルギーに関して世界を牽引している。さらに、太陽光発電の分野でも進展は目覚ましく、2009年に日本の大学で発見されたペロブスカイト太陽電池が世界を席巻している。この太陽電池により、透過性を持つ新しいタイプの太陽電池実現への扉が開かれた。
現在、メガソーラーや屋根置き用途として市販されている太陽電池は、主に結晶シリコン太陽電池である。「結晶シリコン太陽電池には多くの利点がある一方、シリコンウエハをベースとするため、窓などの透明度が必要な面に実装することは加工の面で手間がかかります」と、パナソニック ホールディングス株式会社(大阪府、以下、パナソニック)ペロブスカイト太陽電池の開発責任者である金子幸広氏は説明する。
ペロブスカイト太陽電池をガラス窓に印刷することで、市街地の屋上よりも大きな面積で太陽光を捕捉できる。近いうちに、シリコン太陽電池に近い効率で太陽光をエネルギーに変換できるようになる可能性がある。
ペロブスカイト太陽電池は液体材料を用いて、ガラス上に印刷工法で作製できるという特徴を持つ。高層ビルの多くの垂直面はガラスで構成されており、その面積は屋上で太陽光を捕捉できる面積よりもはるかに大きい。ペロブスカイト太陽電池を窓や壁に組み込むことができれば、都市部で生み出すエネルギーを劇的に増やすことができる。
日本が2050年の脱炭素化目標を達成するためには、毎年東京ドーム1300個分面積相当のメガソーラーを建設しなければならない。「窓や壁に太陽電池を組み込むことで、広い土地は不要となります」と金子氏は語る。
2009年以降、高効率化を目指したペロブスカイト太陽電池の開発が飛躍的に進歩している。ドイツ機械工業産業協会(VDMA)の最近の報告書では、ペロブスカイトは2025年までに商用太陽電池に使われるだろうと予測されている。
この実用化開発の最前線に立っているのは、オックスフォード大学(英国)の物理学教授ヘンリー・スネイス氏によって設立されたオックスフォードPV社や、2020年に804cm²という大型で世界最高の変換効率を樹立し、ガラスを基板としたペロブスカイト太陽電池を開発するパナソニックである。
オックスフォードPV社は、シリコン太陽電池上にペロブスカイトの層を積層することで変換効率を30%近くにまで向上させたが、この方法では、依然として旧来のシリコン太陽電池の制限が残る。
一方、パナソニックは、独自のインクジェット印刷技術とペロブスカイト太陽電池材料に磨きをかけることで、世界最高クラスの変換効率を持つガラスを基板としたペロブスカイト太陽電池の開発に成功している。パナソニックは、ガラスにペロブスカイトを塗布する際の結晶成長を最適化し、基板内で厚さを均一にすることにより、現在市販されている結晶シリコン太陽電池モジュール同等の変換効率を目指している。
学術論文上ではペロブスカイト太陽電池のエネルギー変換効率は26%以上と報告されているが、こうした記録は大面積モジュールではなく、1cm²以下の太陽電池セルで達成されたものである。
金子氏によると、パナソニックは、ペロブスカイト太陽電池の大型化に注力しているという。「一般的に、太陽電池のエネルギー変換効率はサイズが大きくなるにつれて低下します。パナソニックは2020年に、804cm²のペロブスカイト太陽電池モジュールにおいて17.9%のエネルギー変換効率を達成し、そのサイズのペロブスカイト太陽電池の世界記録として米国国立再生可能エネルギー研究所のチャート(NRELチャート)に記載されました」と金子氏は言う。パナソニックは現在、メートル規模の太陽電池の開発へと移行している。
ペロブスカイト太陽電池技術のもう1つの特徴は、製造過程で必要な温度が100℃〜200℃程度と低温であるため、製造時に消費されるエネルギーが少ないことである。現在の結晶シリコン太陽電池の製造過程では、太陽電池用の高純度シリコンを製造する工程等が1000℃以上で行われるため、製造時に使用するエネルギーが多いと金子氏は指摘する。
太陽電池を塗布で製造できることで、さらなる利点もある。「インクジェット印刷の手法を採用することで、どのような基板サイズにも印刷することが可能です」と金子氏は言う。そうした柔軟さが、パナソニックが想定する用途では重要となる。
「建築における窓や壁のサイズは様々です」と金子氏。さらに、レーザースクライビングにより透過度を調整できるため、窓など透過度が必要な個所に適用可能である。一方、壁には透過度のないペロブスカイト太陽電池を適用することができる。しかし、実用化に向けては、ペロブスカイト太陽電池の信頼性向上が課題だと金子氏は言う。ペロブスカイトは特に湿気に弱い。パナソニックは、ガラスにペロブスカイト太陽電池をインクジェット印刷した後、別のガラス板で挟み、湿気を透過させない2枚のガラスの間にペロブスカイトを封じ込めるという手法をとる。また、パナソニックは太陽電池の熱安定性を向上させるため、ペロブスカイト材料に添加剤としてルビジウムやセシウムを使用するなど、材料面でも高信頼性技術の開発を進めている¹。
パナソニックは、2025年に大規模な実証に取り組み、5年以内にペロブスカイト太陽電池を市場に投入したいと考えている。
パナソニックは、脱炭素時代の新たなクリーンエネルギーとして注目されている、グリーン水素製造技術の開発にも積極的だ。グリーン水素は、再生可能エネルギーから得られる電力を用いた水電解による二酸化炭素(CO2)フリーな水素で、石油精製所や工業用アンモニア・メタノールの生産など、様々な用途への利活用が期待できる。現在、これらの産業で使用されている水素は化石燃料を使用して製造されているが、グリーン水素への移行により、CO2排出量を大幅に削減することが可能になる。
「パナソニックは、ペロブスカイト太陽電池、バッテリー、燃料電池などの開発に取り組んでいますが、グリーン水素製造技術の開発が必要であることは明白でした。電解装置の需要予測は非常に膨大です。水素を非エネルギーとエネルギー用途の両方で活用することにより、環境への負荷を軽減し、持続可能な社会の実現に貢献することが期待されています」と開発プロジェクトを主導する可児幸宗氏は語る。
電極触媒には希少な材料がよく使われるが、これには供給不足のリスクがあると可児氏は言う。2018年以来、可児氏率いる開発チームは、貴金属を使用しない、高い電極触媒活性を持つアノード電極触媒を開発した。開発チームは、候補材料を徹底的に調査した結果、豊富に存在していて安価な、ニッケルと鉄から作られた層状複水酸化物と呼ばれる材料を選択した。
可児氏のチームは、ニッケルと鉄からなる層状複水酸化物を用いて、高い活性を持つ電極触媒を開発した。左は陰イオン交換膜型水電解用の膜電極接合体、右はアルカリ水電解用のアノードである。
開発チームは最近、粒径が10nm未満の層状複水酸化物を製造する世界初の方法を確立した²。「我々の層状複水酸化物の活性の高さは、粒径の微細化によって表面積が増加したことに由来します」と可児氏は説明する。また、層状複水酸化物は低温過程で作製されるため、製造プロセスにおけるCO2排出を抑制できる。パナソニックの層状複水酸化物の電極触媒は、アルカリ水電解および陰イオン交換膜型水電解に応用することができる。
現在、このナノ粒子電極触媒の耐久性試験が進行中である。「2025年までに、電解槽メーカーにサンプルを供給したいと考えています。水分解は非常に活発かつ競争の激しい研究分野であるため、開発を加速させなければなりません」と可児氏は言う。
日本は、環境問題への取り組みにおいて世界的なリーダーシップを発揮している。2050年までに海洋プラスチックごみの追加的な汚染をゼロにまで削減するという目標を掲げたことは、その一例だ。この目標に向けて、パナソニックが開発したエコマテリアルが注目されている。この代替品は、従来の化石燃料由来のプラスチックに比べて環境に配慮したものであり、日本がこの問題に取り組む上で重要な役割を果たすことが期待されている。
セルロースファイバー成形複合材料「kinari(キナリ)」は、持続可能な衣類のボタンからコードレススティック掃除機の筐体に至るまで、すでに市場に出回っている。セルロースファイバーは、丈夫で成形可能な複合材料を形成することができ、堆肥化可能な生分解性も持っている上、性能を低下させることなく何度もリサイクルすることができる。
セルロース製造過程を刷新することが、新製品を開発する際の最初の課題だったと、パナソニックのセルロース製品の開発責任者 名木野俊文氏は語る。「木材パルプからセルロースファイバーを抽出する従来の方法は、膨大なエネルギーが必要なのです」と名木野は説明する。セルロースファイバーは、そのファイバーを1本1本に分離する必要があり、これは通常、水処理によって行われる。こうしたファイバーを乾燥させるには多くのエネルギーが必要で、セルロースファイバー1kg当たり2.3kgのCO2を排出する。
名木野氏率いる開発チームは、セルロースファイバーを溶融樹脂で分離・分散させることにより、乾燥する必要をなくした。この過程で発生するCO2は、セルロースファイバー1kg当たりわずか0.5kgだ。このセルロースファイバー複合樹脂ペレットは、製品の成形前に他の樹脂と直接混合することができる。最終的な成形複合材料には少なくとも55%のセルロースが含まれており、70%までの材料をリリースしている。そして、最大85%のセルロースを含む配合物を開発中である。
植物由来のセルロースファイバー成形複合材料「kinari(キナリ)」(左)は、シンプルな容器(右)からコードレススティック掃除機の筐体まで、様々な製品に使われている。
さらに、パナソニックは、リサイクル工程にある様々な種類のプラスチックを、近赤外線分析に基づいて特定・分離するためのプラスチック廃棄物の選別技術を開発した。セルロースは、近赤外線分析下で強い特徴的なピークを示す。このピークを使うことで、リサイクル用のセルロース複合材料の識別が簡単になる。開発チームは、丈夫なセルロースファイバーは複数回のリサイクルに容易に耐え得ることを実証している。「セルロースファイバーは非常に丈夫で、セルロース複合材料は再加工を繰り返しても強度が失われることはありません」と名木野氏は言う。対照的に、ガラスファイバー強化複合材料は、1回のリサイクルで機械的強度が失われると名木野氏は指摘する。
セルロースファイバー複合材料のラインアップをさらに拡大するために、複数のプロジェクトが進行中である。「生産性を向上させて、一般的な樹脂と同じコストで製造できるよう、工程と設備を開発中です。また、コーヒー豆のかす、間伐材、竹などの廃棄物から得られるセルロースファイバーを使用する工程を開発することで、より持続可能なものにしています」と名木野氏。パナソニックのセルロースファイバー複合材料においては、大型家電製品や自動車車部品用も開発中であり、海洋生分解性の開発も手掛けている。「日本が掲げる持続可能な社会の実現に向けた目標を達成するためには、研究開発の成果を社会に受け入れられる価値へと変換し、製品として市場にいち早く投入することが重要です。研究開発自体は持続可能な社会やイノベーションの基盤を築くための重要な一歩ですが、それだけでは十分ではありません」と金子氏は言う。
参考文献
1. Matsui, T. et al. Adv. Mater. 31, 1806823 (2019)
https://onlinelibrary.wiley.com/doi/epdf/10.1002/adma.201806823
2. Koshikawa, H. et al. ACS Catal. 10, 1886 (2020).
https://pubs.acs.org/doi/10.1021/acscatal.9b04505
記事の内容は発表時のものです。
商品の販売終了や、組織の変更などにより、最新の情報と異なる場合がありますので、ご了承ください。