
2024.03.22
パナソニックグループのひと
新時代のモノづくりで、乾電池事業の未来を拓く
:鈴木 冬馬
シリーズ:
全ての社員を幸せにするために、自らの殻を破り
「
」
をUNLOCK!
工場の物流改革に挑む若きリーダー
鈴木 冬馬
パナソニック エナジー株式会社 エナジーデバイス事業部
コンシューマーエナジービジネスユニット モノづくり総括 生産技術部
すずき・とうま 2016年入社。乾電池を生産する守口工場で生産設備の保全、設計・開発に携わる。2020年にグローバルモノづくり推進部に異動し、タイをはじめ海外生産拠点の新規設備導入を手掛ける。2022年から現職。乾電池事業の未来を拓くモノづくり体制の構築に挑戦し続けている。
現場の声に寄り添う
自動搬送システム
で築くスマートな生産体制
乾電池の国内需要を90年以上にわたり支えてきた守口工場(大阪府守口市)での生産を終了し、二色の浜工場(大阪府貝塚市)に移管するプロジェクトが2020年からスタートしました。私はその中心メンバーの一人として参画。敷地面積の拡大に伴って製品の構内運搬距離が長くなることから、自動搬送システムや自動倉庫システムなど、新たなモノづくりの仕組みを導入し、リードタイム短縮や在庫削減、省人化に取り組みました。

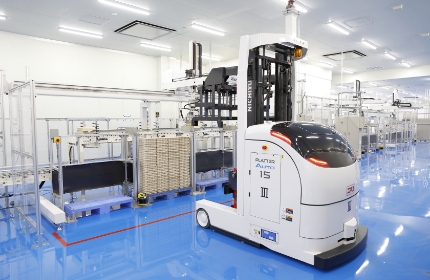
大規模な工場に自動搬送システムを導入するのは、当社にとっても大きな挑戦でした。「やりたい」と自ら手を挙げて担当になり、まずは必要な知識を得るためにインフラ関連のメーカーに指導を仰ぐなど、基礎を学ぶことから始めました。現場では、自動搬送システムの導入に対する抵抗や不安の声も上がりましたが、詳しく話を聞いてみると、変化に対してネガティブなのではなく、システムの複雑な操作方法やオペレーションによる影響を懸念するものがほとんどでした。どんな意見も素直に受け止め、その思いをしっかり理解し、最適なコミュニケーションを図ることが大切だと考え、初期の段階で現場の社員と一緒に設備メーカーの工場を訪問。自動搬送システムを実際に体験してもらい、二色の浜工場に導入したときの完成形をイメージしてもらうことで、少しずつ理解と共感を広げていきました。また、以前の守口工場は運搬距離が短く、ムダや課題が表面化しにくい環境だったので、この機会に現場の社員に密着し、負荷がかかっている部分や不要な作業がないかを調査。課題を見える化したことで、今まで見過ごされていた生産体制の根本的な課題に工場全体が向き合うようになりました。
こうした取り組みのベースにあるのは、「生産性を上げるために設備の設計・開発を行うわれわれにとって、製造現場の社員はお客様」という入社当時に先輩から教わった考え方。たとえパナソニックグループの仲間であっても、お客様として向き合うことで、より良いものを作ることができると考えています。常にお客様起点で考え、ささいなことでも可能な限り意見を集約しようと心がけました。
現場をもっと楽にしたい
自らの学びを広げて自動化に挑む
約3年かけてプロジェクトを完遂し、2023年11月に二色の浜工場が本格稼働を始めました。この挑戦を通じて痛感したのは、モノづくりは設備だけを見ていてもダメで、在庫管理や物流など、サプライチェーンの全体像を把握しなければ、本当に必要な生産能力を見極めることはできないということ。また、工場全体の自動化実現に向けて、異なる建物の間を自動搬送するためには、スムーズに往来するための導線設計など、より広い視野で知識を身に付けなければならないことも学びました。その都度、担当部門とやり取りを重ねたり、自ら調べたりしながら進めていきましたが、手探りな部分も多く、これで良いのかという不安は常にありました。ただ、うまくいかなくても、「これではできない」ということが分かったんだとプラスに捉えると、失敗も貴重な財産になります。新しいことや難しいことに挑戦すれば、壁や困難にぶつかるのは当たり前。日頃から自分に足りないものや補うべき点を考えながら、答えを探していくプロセスを楽しむように心がけています。

人に依存しないスマートな生産体制の構築を目指した二色の浜工場では、80%超の自動化を実現しました。一方、さまざまな分野の知識や視点を学んだことで、新たな課題も浮かび上がっています。今後も、現場の作業負荷を低減することに加え、より創造的な仕事にチャレンジできる環境を構築し、乾電池のモノづくりに関わる社員の「幸せの、チカラに。」なれるように挑戦を続けていきます。
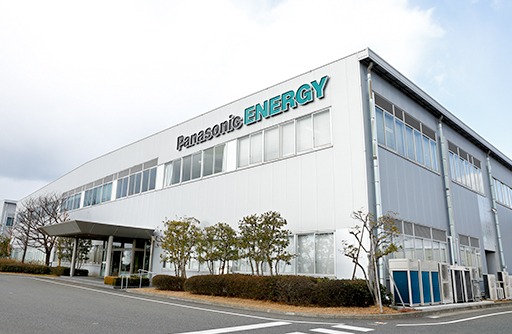
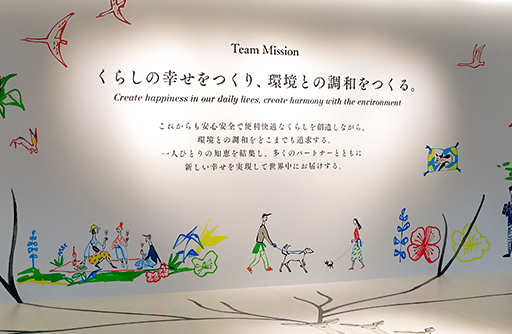
乾電池事業の未来を拓く「グローバル旗艦工場」の二色の浜工場。自動搬送システムによるスマートな生産体制を構築しただけでなく、再生可能エネルギーの最大活用で、CO₂排出実質ゼロを達成。また、太陽光発電導入の取り組みが評価され、令和5年度 新エネ大賞 経済産業大臣賞も受賞した。さらに、小学生を対象とした工場見学や手づくり乾電池教室の開催などの活動を通じ、地域や社会に開かれた魅力ある工場を目指して進化を続けていく。
記事の内容は公開時のものです。
商品の販売終了や、組織の変更などにより、最新の情報と異なる場合がありますので、ご了承ください。
More from this series
シリーズ記事
Recommended articles
おすすめ記事