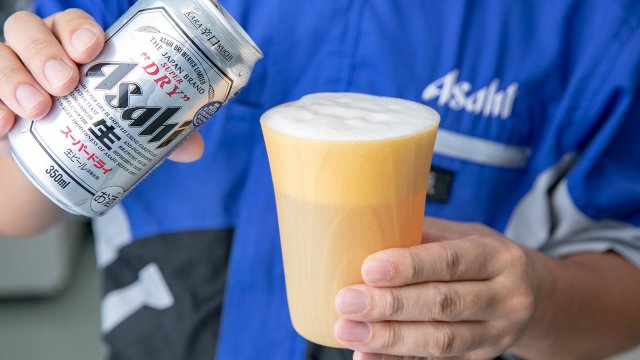
Plastic waste in the oceans, depleting oil resources and climate change are all environmental concerns, but lately there has been a lot of noise from all corners of the globe to reduce the amount of plastics in the world. This article looks into a next-generation material that might just do that. It reports the background to development and the future prospects of a moldable resin developed with plant-derived "cellulose fiber" by Panasonic and the reusable "Forest Tumbler" jointly developed from the resin by Panasonic and Asahi Breweries, as told by the people in charge at both companies.
Summary
- Panasonic has developed an "environment-friendly" resin made of plant-derived "cellulose fiber."
- Having drawn the interest of Asahi Breweries, the two companies jointly developed the material into a reusable cup that has already met with great reviews at various events.
- What went on behind the scenes at both companies that led to development and what do the engineers at Panasonic think is so great about this cellulose fiber resin?
Using the cellulose fiber found in trees as a molding material
Ever since the United Nations General Assembly adopted Sustainable Development Goals (SDGs) for the planet in 2015, the world has steered its rudder more and more in the direction of sustainability. These SDGs address a wide range of topics, but solving environmental issues like the plastic waste in the world's oceans is an urgent theme they raise.
In the midst of all of that, Japan's Ministry of the Environment has had its eyes focused on plant-derived "Cellulose Nano Fiber (CNF)" as a next-generation bio material. CNF is a refined version of the natural fiber found in all trees. Because of its ubiquitous nature, it offers promise as a sustainable resource of low environmental load since it can be effectively recovered from forest resources like wood from thinning and plant resources contained in industrial waste.
Research and development that has been underway since the mid-2000s has finally advanced to the practical application stage in recent years. Encouraged by the progress, the Ministry of the Environment has been promoting a model project centered on CNF since 2015. Panasonic was named one of the businesses involved in the project and was entrusted, between 2015-2017, with "developing technology for reducing CO2 emissions from CNF production processes" and, between 2016-2017, with "testing performance and verifying the practical use of CNF in home appliance products."
Using what it had learned in these projects, Panasonic launched its "POWER CORDLESS" stick vacuum cleaner with some parts made of the new lightweight "cellulose fiber resin" in August 2018. It was the first such example of use in Japan with a home appliance. Then, in July 2019, a high-density molding material that incorporated upwards of 55% cellulose fiber into the base resin was developed. Because it is made mostly of natural materials, less plastic is obviously used. Moreover, it is white, which enhances coloring freedom, but Panasonic used proprietary molding technology to create the warm look of wood.
Eventually, Asahi Breweries caught sight of this SDG-compliant, "environment-friendly material" and teamed up with Panasonic to develop it into a reusable cup for drinking beer. It was completed in July 2019 and christened the "Forest Tumbler."
A challenge that began with the determination to make a "nondisposable" cup
The two companies met at a technology exchange hosted by Panasonic in July 2018. Responsible for bridging the gaps between attendees, Panasonic's Kengo Fukuma recalled, "Since both companies were Olympic-Paralympic Partners (Panasonic: Official Worldwide Partner; Asahi Breweries: Tokyo 2020 Gold Partner), we planned a technology exchange to bounce technologies and ideas off each other in search of possible new areas of business. We showcased a variety of technologies, but they were particularly interested in our resin material that contained cellulose fiber."
Kengo Fukuma
Chief, Solution Team No. 2, Sales & Marketing Dept.
Business Solutions Division
Panasonic Corporation
A big reaction came from Toru Kohara of Asahi Breweries. Because he was engaged in researching and developing containers and packaging at his company, Mr. Kohara had strong interest in container recycling and environment-friendliness. The two companies met at a time when, as Mr. Kohara put it, Asahi Breweries "was searching for a truly environment-friendly material" as the opportunities spawned by the UN's SDGs were growing in the leadup to the Tokyo 2020 Games.
Mr. Kohara explained, "Every year, some 12 million plastic cups bearing the Asahi Breweries logo are consumed and, if you include the unmarked cups, there are even more. Because of those numbers, we are regularly thinking about how we could go about making a nondisposable cup."
He continued, "But, then, when I saw the cellulose fiber resin, it hit me that we could possibly make a cup with it. We had long been searching for a material whose value would resonate with customers, but this resin was additionally interesting because it could be used repeatedly. To begin with, the look and texture of wood have very high emotional value. Plus, I research containers that give beer a good head and, since cellulose fiber resin contains plant fiber, there are tiny undulations on the surface, which we expected to add to the head. For these two reasons, I said, 'let's make a reusable beer cup' right there on the spot."
Toru Kohara
Assistant Section Manager, Department of Packaging Technology
Research & Development Laboratories for Packaging Technology
Innovation Headquarters
Asahi Breweries, Ltd.
After that, things transcended much more quickly than would be expected in a collaborative project between two top businesses. For Mr. Kohara, it was almost a daily ritual to be on the phone with the Panasonic engineers in Osaka. Because it contained plant fiber, the cellulose fiber resin did not flow smoothly into the mold and it did not lend itself to thinning, but Asahi Breweries was adamant about making the cup thin enough that the beer could be seen from the outside. Mr. Kohara explained, "We wanted to be able to see the border between the beer and the head from the outside when pouring the beer. It would amaze the customer for one, because it would be see-through even though it's wood, and it would reassure the customer how much beer is in his cup at a glance."
Efforts focused on making the border between the head and beer visible from the outside when pouring
Additionally, Mr. Kohara requested that the cup have irregularities. Conventionally, with molded products, the theory is the exact opposite: the product is defective if there are irregularities. But, Asahi Breweries wanted the Forest Tumbler to have the added value of a personal tumbler that, being unique unto itself, would inspire people to use it repeatedly. On that note, the engineers at Panasonic carefully controlled molding in order to make highly original tumblers.
They also got a "scent" as a sort of byproduct. When a person grabs a Forest Tumbler, a faint sweet scent derived from timber is released, so the user gets a whiff of nature that he or she can enjoy by way of his or her sense of smell. As Mr. Fukuma told, "The scent actually drove us from Panasonic crazy. Because, you see, it is not standard practice in our world for a material to retain a smell. Still, Mr. Kohara described it as a positive scent that goes well with beer and, went as far as to ask that it be left in the cup." In fact, it can be considered a good example of value being spawned by changing how one looks at things.
In any case, as a result of continuous uncompromising prototyping, the very first sample was finished in just a half-year's time from the technology exchange. And, sample cups were raised by the teams from Asahi Breweries and Panasonic for the toast celebrating the completion. Mr. Kohara recalled that day vividly: "The look and texture were givens and, when the beer was poured and sipped, it was creamy and went down better than expected. Corroboration came when the head was found in proprietary testing at Asahi Breweries to contain bubbles 1/5 the size of those formed in ordinary plastic cups. We had gotten this far, so just there was one more step - verification. Those tests were integrated into events, as we were getting eager to release the cup as soon as possible."
Shortly after that, in March 2019, test research was conducted during cherry-blossom season at an event adjacent to Asahi Breweries' headquarters in Sumida-ku, Tokyo. Between then and now, it has been sold on limited occasions like home games played by J League soccer club Gamba Osaka and the Tsukuba Craft Beer Fest 2019, but has received positive reviews from those who bought it. As Mr. Kohara recounted, "Over the three days of the Tsukuba Craft Beer Fest, we handed out 4,000 cups and, because they were repeatedly used at the site, reduced the use of about 15,000 disposable plastic cups. The reactions we got were very positive and gave you a sense that people, especially the younger generation, were well aware of SDGs. When looked at outdoors, it seems so much more like wood because the sunlight passes through it. As a product, it's an eyecatcher."
There was not a single negative opinion of the project in either company. And, now that the verification phase was done, Asahi Breweries put together a project team with sights set on full business development. In Mr. Kohara's words, "Right now, we are at the deciding point that will determine how it all will unfold as a tangible, sustainable business next year and beyond." As he explained, the Forest Tumbler would be positioned along an axis of ESG (Environment, Society and Governance), not pursued as a profitable business through sales in tandem with the company's Super Dry brand of beer.
He added, "Our future goal is to do away with 'disposable' behavior in and unto itself. Changing consumer behavior is what I call 'innovation' and, with the influence we have on the industry, it is significant in terms of sending the message and arousing awareness that we do it first."
Mr. Fukuma looked at it a bit differently: "Because this cup got us into a field we had never challenged until now, we want to carefully and assiduously expand this category. At the same time, we want to continue this business as a social contribution activity until a 'reusable' culture penetrates society, since, as our founder Konosuke Matsushita said, 'A company is a public entity of society,' and that DNA lives on in our workforce today."
Panasonic continues to explore higher density versions of the cellulous fiber with the notion of eventually kneading in and recycling the bio-sourced business waste discarded by Asahi Breweries.
Twice the advantages in an abundance of resources available and less CO2 emissions
Though the Forest Tumbler began as a model project of the Ministry of the Environment, Panasonic's Manufacturing Innovation Division had already been working on a cellulose fiber resin for some time. As the Division's own Masashi Hamabe pointed out, "We had been pursuing cellulose fiber as an alternative material to glass fiber and synthetic fiber well before that."
He continued, "The trend to move away from glass has been picking up speed in the West because, even if the glass fiber is incinerated, the glass still remains and necessarily ends up in a landfill site. There is also the demerit of it losing its strength under repeated use. On the other hand, compared to other fiber-reinforced resins, cellulose fiber is fat at its core, which gives it high elasticity, and thin at the tip, which minimizes cracking under stress. These characteristics make it strong against surface impacts and light in weight as a resin. And, because it is plant fiber, nothing is left over when it is incinerated, and, the fiber doesn't break, which makes it advantageous from a recycle perspective."
Masashi Hamabe
Staff Engineer, Thin Film & Material Processing Technology Section
Material & Device Technology Dept.
Manufacturing Solution Center
Manufacturing Innovation Division
Panasonic Corporation
The most practiced conventional way to defibrate cellulose fiber is in water, but to then compound the fiber into a resin, drying is needed, which increases energy costs and CO2 emissions. In the first project for the Ministry of the Environment, Panasonic developed a completely dry defibration process that did not use water and decreased the number of steps, which translated into lower costs and improved productivity. Furthermore, it reduced 1.8 kg of CO2 per kg of cellulose. Shoma Nishino of Panasonic's Manufacturing Innovation Division took those results to the next phase of "mounting it on society."
As he explained, "There is always the idea that lowering costs gets you closer to practical application. The cellulose fiber resin was similar to reinforced resin that was already being used with Panasonic products and, in some ways, was even better, so in the next model project, we verified its applicability to refrigerator and washing machine parts. Those verifications paved the way to its adoption with a cordless stick vacuum cleaner that was released in August 2018."
Shoma Nishino
Staff Engineer, Development Sect. No. 2
Mold & Die Technology Center, Advanced Molding Technology Dept.
Manufacturing Innovation Division
Panasonic Corporation
For the reinforcing materials, the opposite approach was taken from that for the reusable cup. The resin could not have inconsistencies and discoloring was prohibited. Moreover, as the reinforcing material was to be used for industrial products, poor yield would hinder manufacturing. Summarizing the team's feelings, Mr. Nishino recounted, "When the material was to be used for a vacuum cleaner, we did test after test out of fear that the color would change before it was all over. Nevertheless, I was very happy to have contributed to the first application in the home appliance industry and came away from it all with a solid sense of accomplishment."
The next challenge will be higher density versions of the cellulose fiber. While showing some prototype pellets, Masayoshi Imanishi of Panasonic's Manufacturing Innovation Division explained, "The most cellulose fiber we've included so far is up to the 85% level. We've also been successful at keeping the product white even at higher concentrations. This gives more freedom to color products, which should be a big sales point."
The color of the prototype pellets (middle row) does not change even when cellulose fiber content is increased. This speaks to the high degree of coloring freedom.
Though the plant-derived reusable cup and the environment-friendly reinforcing material for industrial products look completely different, they have the same roots and both have the potential for becoming leading materials in the SDG age. Even the engineers who have been involved in development are excited by the potential, as Mr. Hamabe expressed, "Society can become more environment-friendly and sustainable by expanding the uses of this material." Mr. Imanishi phrased it as, "Environment-friendly materials like this should be more prevalent in daily lives and a standard of living." And, Mr. Nishino highlighted the practical aspects of a "resin that looks like wood, as it could be used in all sorts of applications that appeal to esthetic sensibility and appreciation."
Masayoshi Imanishi
Thin Film & Material Processing Technology Section
Material & Device Technology Dept.
Manufacturing Solution Center
Manufacturing Innovation Division
Panasonic Corporation
Mr. Kohara of Asahi Breweries summarized his company's view as, "We do not think of the product as finished. Like software, it needs to be updated and upgraded." That kind of passionate thinking finds the right engineering answers at Panasonic. With the goal of putting the cellulose fiber resin to practical use having been reached, what everyone is hoping for now is for it to spread far and wide as a material of the 21st century.
- Reproduced from the website "Mirai-kotohajime," by courtesy of Nikkei Business Publications, Inc.
# # #
- Disclaimer:
- We would like to note that Panasonic Newsroom is not a place to address personal Customer Service issues. Even though this is not the forum, Panasonic is always eager to resolve your concerns. Our local customer services contacts can be found at Global Support or you can see our list of Social Media Accounts to find the right channel for your queries and concerns.
Related Links
Related News
- How the "Kid Witness News" Video Production Program Has Supported the Dreams and Potential of Kids Around the World for 30 Years (Nov 05, 2019)
- Conserve Marine Environment through Its Corporate Cafeterias - Panasonic's Challenge to Propagating Sustainable Seafood (Aug 02, 2019)
- Sifting through Resources Is Like a "Treasure Hunting": The Job Asked of Panasonic's State-of-the-Art Electric Appliance Recycling Facility (Jun 11, 2019)