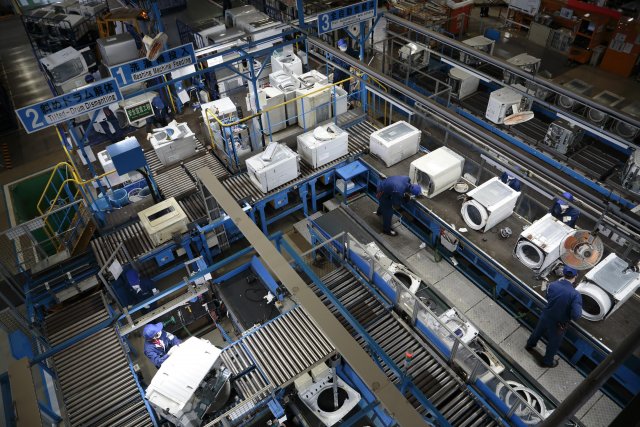
The Panasonic Eco Technology Center or PETEC, as most people call it, is located in Kato City, Hyogo Prefecture, Japan. There, using the latest technologies, they are recovering resources from electric appliances as part of Panasonic's global effort to promote recycle-oriented manufacturing, under an intriguing yet appropriate motto of "Treasure Hunting." For this article, PETEC President Hiroki Kono talked about what they do at this state-of-the-art electric appliance recycling facility.
Summary of this article:
- Since Japan's Home Appliance Recycling Law went into effect in 2001, the Panasonic Eco Technology Center (PETEC) has processed over 14.5 million appliances.
- With Panasonic founder Konosuke Matsushita's words "Learn not to waste but to appreciate the worth of materials" echoing through the halls, PETEC aspires to build a recycle-oriented society where resources are passed along "from product to product."
- Over 186,000 people from 131 countries and regions around the world have toured PETEC as of the end of March 2019.
Echoing Throughout the Halls the Guiding Message of "Learn Not to Waste but to Appreciate the Worth of Materials"
The campaign to protect and conserve the global environment has grown markedly in Japan over these past few years, as indicated by the SDGs (Sustainable Development Goals) the government is pushing and the sizeable investment in ESG (environmental, social and governance) by private businesses. Japan's Law for Recycling of Specified Kinds of Home Appliances (commonly referred to as the "Home Appliance Recycling Law") was also considered ahead of the times when it went into effect in 2001.
Now, 18 years later, it is common practice across the country with air conditioners, TVs, washers and dryers, and refrigerators and freezers to follow prescribed procedures to have these appliances properly recycled. However, though consumers use these appliances up until discarding them, there are few people who know what happens to them after that.
This is a story about a facility that recycles these appliances when no longer useful.
Panasonic has been operating the Panasonic Eco Technology Center (PETEC) in Kato City, Hyogo Prefecture since Japan's Home Appliance Recycling Law went into effect in 2001. There, in just FY2018 alone, about 940,000 used electric appliances from 6 prefectures (Osaka, Kyoto, Hyogo, Nara, Shiga and Wakayama) were brought and processed. Since PETEC began operations, they have processed over 14.5 million appliances.
Several tens of trucks worth of used appliances are transported to PETEC every day.
Under Japan's appliance recycle system, manufacturers whose products are collected and recycled are divided into two groups, A and B. PETEC handles Group A to which belong Panasonic, Toshiba, Samsung Electronics Japan, Daikin Industries and others (Group B includes Hitachi, Sony, Sharp and others). And, though they accept used appliances of multiple manufacturers, PETEC was established entirely with capital from Panasonic.
The reason for that lies in the guiding words of Panasonic founder Konosuke Matsushita, who was gravely saddened by the environmental destruction pollution was already causing around the world when Japan was right in the middle of a highly welcomed period of strong economic growth that straddled the 1960s and 70s. The edict "Learn not to waste but to appreciate the worth of materials" he formulated from that is alive and well within Panasonic to this day, which explains why PETEC's founding was timed to coincide with the enforcement of Japan's Home Appliance Recycling Law.
The motto at PETEC is "Treasure Hunting." The treasure they are talking about is the trove of still viable resources lying dormant in the mountains of used appliances that are collected and delivered to them every day. Considering that - and these are just representative examples - liquid crystal and plasma TVs are 46% iron, 1% copper and 4% aluminum, washers and dryers are 48% iron, 2% copper and 2% aluminum, air conditioners are 30% iron, 7% copper and 9% aluminum, and refrigerators and freezers are 50% iron, 2% copper and 1% aluminum, there are a lot recyclable resources buried in these products. PETEC's mission is to carefully sort, recover and then supply these resources as materials for new products.
(Source: "2018 (17th term) Annual Report on Electric Appliance Recycling," Association for Electric Home Appliances)
Used electric appliances are efficiently disassembled by dividing up the work on "disassembly" lines.
Panasonic's Technologies Are Used to the Fullest to Recycle Valuable Resources
As Hiroki Kono, President of PETEC, explained, "We take used electric appliances, sort them and effectively use the resources we recover from them as resources once again." Used appliances contain not only metals like the iron, aluminum and copper mentioned earlier but also rare precious metals as well. This is precisely why they are called "urban mines."
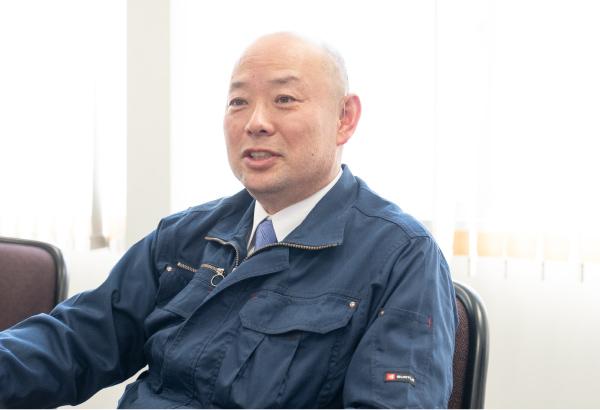
Hiroki Kono
President, Panasonic Eco Technology Center Co., Ltd.
Chemically synthesized plastics are being constructively used, too. In fact, amongst Panasonic products, plastics are being recycled for refrigerator parts, bottom frames of washing machines and other uses. Moreover, having introduced equipment for converting plastic that was previously discarded as waste into solid fuel, PETEC is engaged in recycling from end to end. This mindset that wants to contribute to a budding recycle-oriented society ties into the company's vision of passing resources along "from product to product."
To make an analogy, if a plant that makes electric appliances is compared to an "artery," then PETEC's base of operations is the "vein." With that dichotomy established, it should be obvious that different technologies and know-how from what are used on the arterial side are needed to disassemble and break down dexterously assembled products and recycle them as valuable resources on the venal side.
As one example thereof, Mr. Kono pointed to the "High-Precision Resin Sorting System" that Panasonic developed. The system sorts various types of plastic at high speed by shining an infrared beam on the crushed material and instantly measuring the rebounded wavelength to determine whether the plastic is PS (Polystyrene), PP (Polypropylene) or ABS (Acrylonitrile-Butadiene-Styrene). It sorts the plastic at the same time by blowing air at a fast flowrate.
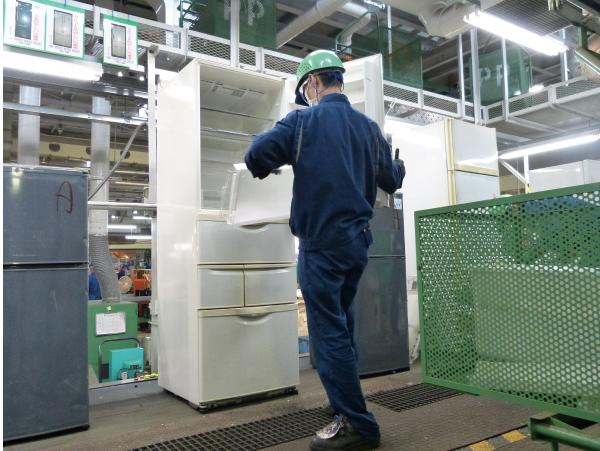
Refrigerator disassembly line. Parts are removed from inside the refrigerator by hand.
Mr. Kono added, "The fact that there is a system that simultaneously separates three kinds of plastic and at high speed, too, is because of Panasonic in my opinion. Panasonic's arsenal of technologies is packed into an algorithm that analyzes the floating trajectories of resin dust. Here, because a large number of used appliances are brought in every day from six prefectures, processing speed is of the essence. We improved our productivity in leaps and bounds by successfully sorting out individual materials to a high degree of precision."
Nonetheless, esthetics are nowadays a key feature of many products, for which reason alone material sorting now demands more man-hours in some cases. In that regards, Mr. Kono projected his future outlook by noting that "Panasonic has great image analysis and robotic technologies, so we should be able to improve efficiency via AI and IoT."
Moreover, PETEC has and continues to propose eco-friendly design based on the 3R's (Reduce, Reuse, Recycle) to the arterial side by letting the recycling forefront speak for itself. As Mr. Kono explained, "We get people from Panasonic's development and design departments to come out here to see recovery and sorting in action and then talk with us about designing and manufacturing products that are easy to recycle to begin with." These exchanges have brought about all kinds of improvements such as replacing mounted name plates with laser printing, labeling materials so as to prevent confusion when sorting them, and using rust-free screws.
Building Awareness of the Importance of Resource Recycling Begins with Fun Plant Tours for Kids
Before getting any sort of explanation, a tour is given of the plant, where, to anyone's surprise, the lines are in no way inferior to those on the arterial side, although the process looks reversed. Work starts by removing screws, dismantling the appliance piece by piece from there. There are steps that have to be done manually, but most of the process is machine-automated, so work proceeds methodically.
They use an exceptional amount of air also for the work environments where there are people. Reason being, an outdoor unit of an air conditioner that has, for example, been exposed to the elements for almost ten years will be dirty and covered in dust. So, they modified their air conditioner line in 2018 to thoroughly remove dust by trapping it with a powerful airblow before assist robots transport and dismantle the heavy units. They also circulate fresh air along the line in order to do away with the strenuous factors of work as best possible.
Mr. Kono pointed out that "A lot of people probably imagine something 'dirty' when they hear the word 'recycle plant.' But, just about everybody who tours the plant comes away thinking 'that was pretty clean' and 'with all of the machinery, they are efficiently recovering resources.' At PETEC, we want everyone to know that we practice the 5S's (seiri [sort], seiton [straighten up], seiso [clean], seiketsu [standardize cleaning practices] and shitsuke [sustain by disciple]) and are eco-friendly in how we operate."
Kato City, where the plant is located, is one of the largest producing regions of Yamadanishiki, the brand of rice used to make Japanese sake. Situated amidst a picturesque landscape of rice paddies, the facility has a clean look that, from the outside, does not suggest your typical recycling plant. PETEC desires nothing more than to blend into the surroundings, which is why they meet with community leaders and experts once every three months to discuss environmental conservation.
The plant tours given every Tuesday through Friday are instrumental towards gaining a proper understanding of resource recycling amongst the general public. Every year, some 10,000 people ranging from upper-elementary students to adults from all walks in life visit PETEC, which, over the years, has added up to about 186,000 visitors. Many have come from overseas as well, hailing from 131 countries and territories around the world as of April 16, 2019. As Ms. Minori Fujiwara, who is in charge of tours for PETEC's Administration Department, explains, "It is truly worth seeing the process that transforms a faithful home appliance one grew fond of over the years into new resources. So much so, we have recently become a destination for school trips. And, we are happy to teach people, young and old, about the importance of recycling."
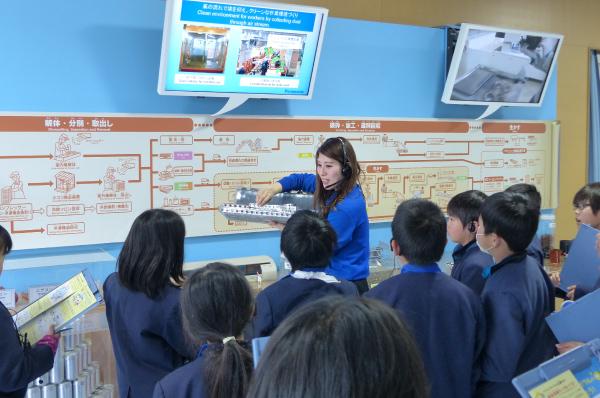
Minori Fujiwara
Tour Leader, Administration Department
Panasonic Eco Technology Center Co., Ltd.
Mr. Kono concurred that this kind messaging is critical for PETEC.
As he put it, "There have been kids amongst those who took the tour that said this was the kind of job they wanted to do in the future. We want more repeaters who come back every year to see for themselves how PETEC keeps evolving. Moving forward, SDGs will be front and center, and protecting the global environment will naturally be one of the important themes therein. In other words, what we are doing will have to be done farther and wider. I'd like people to think of PETEC as a place that is doing precisely what the world needs."
Panasonic has purposely made environmental activities an integral part of the corporate code of conduct, as seen by its Environmental Declaration in 1991, the Green Plan 2018 in the leadup to the company's 100th anniversary and other policies. Now marking its 19th year of business, this long-standing hallmark to recycle-oriented manufacturing might provide a hint as to which direction to head from here.
A gallery has been built specifically for visitors to safely enjoy a commanding view of the plant floor below.
- Reproduced from the website "Mirai-kotohajime," by courtesy of Nikkei Business Publications, Inc.
# # #
- Disclaimer:
- We would like to note that Panasonic Newsroom is not a place to address personal Customer Service issues. Even though this is not the forum, Panasonic is always eager to resolve your concerns. Our local customer services contacts can be found at Global Support or you can see our list of Social Media Accounts to find the right channel for your queries and concerns.
Related Links
Related News
- [Press Release] Panasonic Realizes Its First Zero-CO2 Factories* at Two Sites in Japan and Europe under 'Panasonic Environment Vision 2050' (Feb 28, 2019)
- Panasonic Utilizes 100% Renewable Energy to Power the Consumer Electronics Recycling Plant (Dec 06, 2018)
- Panasonic "Annual Report 2018" and CSR/Environmental Report Published (Aug 31, 2018)