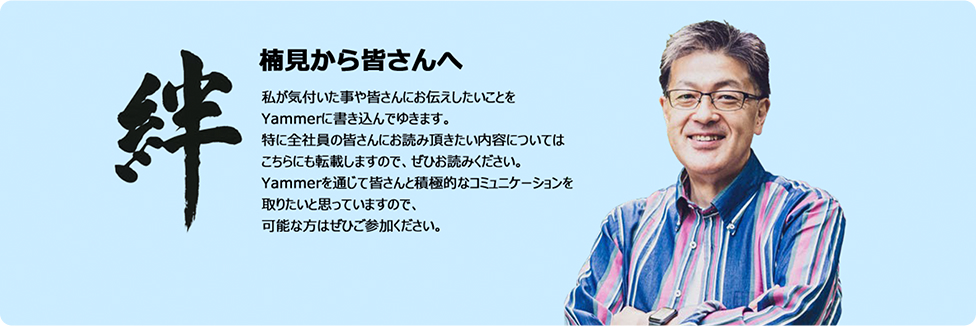
2023年8月22日
LAS社 ランドリー・クリーナー事業部 静岡工場に3度目の訪問(8/1)
皆さん、おはようございます。
8月1日(火)に洗濯機の静岡工場を訪問しました。旧AP社の事業担当時代を除き、グループCEOになってから3回目の訪問となり、グループ製造拠点の中で最も頻繁に訪れていることになります。
前回の訪問は昨年6月28日です。その時の訪問記にも、昨年は昨年で「期待どおりの進化を遂げていただいた」と記した一方で、徹底して正味率視点での課題形成をお願いしました。
そして、今回の訪問では、カイゼン活動にさらに魂が入り、大きな成果も出ていることを確認することができました。
1点目は、静岡固有の場所の制約に対し、仕掛在庫を軽減しつつ源泉の可動率を確保、組立工程でも非稼働時間を徹底削減(=可動率アップ)し、結果として日々完結率(1ヶ月の中での日々の計画生産数を達成した割合)の高位安定とそれによる即納率の向上につなげています。昨年の6月の日々完結率が66%であったのが今年の6月では90%を記録、DBM(Dynamic Buffer Management)の導入も相まって1年前は50%未満であったドラム洗の即納率は97%にまで向上しています。
工場としては、今年度は特に仕掛在庫を軽減しつつ(=源泉工程の機種切替はどうしても多くなる)可動率に徹底的に拘って活動してくれています。その可動率を全員の共通理解とするために、可動率の向上を阻む非稼働要因・ロス要因のチャートを工程や大部屋のWIPボードの横に掲示して全員の共通認識化を図っています。
これによって、請負の方も含めて現場の皆さんが、自分の作業のどういうところが可動率に影響を与えるかがわかるし、可動率80%というKPI目標に対して、個々の作業へのKPIのドリルダウンができる。これはグループの中でも模範的な取り組みではないかと思います。
2点目は、WIPボートと大部屋活動が大きく進化していたこと。WIPボード自体も通り一辺倒ではなく、目標と現状を数字できっちりと見える化して、それを共通理解とすべく、WIPボードの運用とフォーマットを同時に進化させています(写真①)。しかも、目標・実績をしっかり共有する小部屋と、工場全体の日々の課題解決の場である大部屋の役割を分けながらも、各工程のWIPボードが大部屋のWIPボードときちんと連結して運用しています。
大部屋ではディスプレイ3枚のコクピットが設置されていました(写真②)。1つのディスプレイには30分ごとの各工程の生産の状況が表示されていますが、異常が起きているところは、そこをクリックして深掘りして詳しく状況を調べることができる。これは異常への対応のスピードを上げるために非常に役に立っていると思います。
3点目は需要連動生産。これは口を酸っぱくして「やってみてください」とお願いしていたことですが、Onebeatを活用してDBMを導入し、量販1法人との実証実験で、途中、運用やロジでの苦労もありましたが、ほぼ想定通りの成果をあげて頂きました。この件では、ファーストペンギンを買って出てくれたことに感謝あるのみです。
今回の訪問で、活動開始当初にやって頂きたかった事をほぼやって頂いたことが確認できました。しかし、「改善後は改善前」。これで終わりではありません。静岡の皆さんには、今回の訪問で私が気づいたことを3つ共有しました。
1点目は製造DXのさらなる進化。静岡工場では元々、加工条件と不具合の紐づけを去年からやっていただいていますが、当たりをつけてやるのではなく、より多くのデータを使ってAI等を活用しながら相関性分析する。あるいは、工場がフル生産のときと比べて生産の空いているときに、まとめ生産をするべきか、こまめに切替生産をやるべきか等の最適化には、まだチャレンジの余地があるのではないかと感じました。
2点目は人生産性の考え方。日々完結率が100に近づいたからといって断じて完成間近ではありません。当社では、人生産性を一人あたりの生産台数という見方をしますが、トヨタでは一人ひとりの正味率という考え方をします。今回、静岡工場で「正味率はどれくらいか?」と尋ねると「12~14%くらいです」と即座に答えが返ってきました。これを即答された拠点は初めてで、そのことだけでも取り組みが進みつつあると感心したのですが、作業時間の86~88%は正味付加価値をつけていない、いわゆる7つのムダに時間を費やしているということになります。まさに、「1秒・1歩」に拘って工程を見直すことで改善の機会が生まれるところ。ここは訪問後の皆さんとの懇親会でも盛り上がり(?)、「まずは20%を目指そう」ということになりました。
3点目は需要連動の取り組みの展開の加速。これは洗濯機にとどまらず、また量販1法人にとどまらず、早く展開すれば、営業CFに面積で効きますので。ただ、そのためには同時に設計段階での部品の共用化を徹底して進めなければ、部材在庫を多めに構える羽目になりかねません。従って設計・製造・調達連携を加速いただく必要があります。
この2年間の静岡工場の大きな進化、やはり皆で力を合わせればできるのだという確信をさらに強めました。そして静岡の皆さんの熱気からは、大野耐一様のお言葉でもある「かくすれば、かくなるものとわかりなば、やむにやまれぬ改善魂」の域に達してきているな、とも感じました。
こうなると、改善は止まらないはず。
次は、正味率20%に進化した静岡の訪問が楽しみです。

写真①:WIPボードの進化

写真②:大部屋のコクピット
※このサイトはパナソニックグループで働く皆さんが、ご自身のワークスタイルやライフスタイルに合わせて、イントラネットにアクセスできない状況でもグループの情報に触れることができる環境を構築することを目的としています。
本ページのURLや、掲載されているコンテンツを許可なく外部と共有したり、SNS等に掲載したりすることのないよう、取扱いは十分ご注意ください。