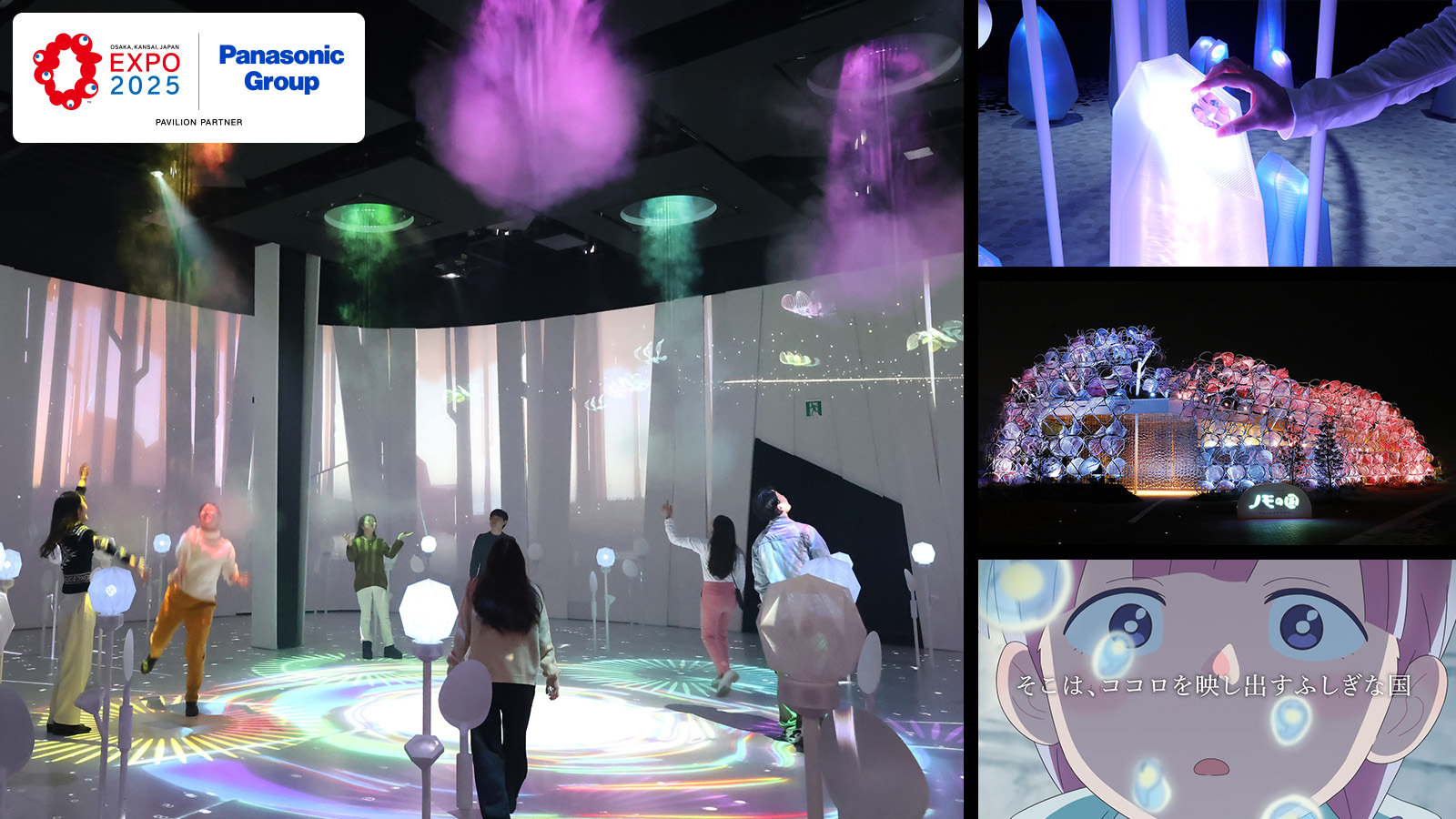
Mar 31, 2025
- Company
- Feature Story
- Panasonic GREEN IMPACT
- EXPO 2025
The texts contents of this article were originally produced in partnership with Nature Portfolio as an advertisement feature and published on 1 September 2023 in the online version of Nature (nature.com), a weekly international journal publishing the finest peer-reviewed research in science and technology. This article introduces the full copy of the advertisement feature for Panasonic Newsroom Global readers. (For the original article, visit: Three sustainable Japanese technologies to watch (nature.com))
Researchers are making progress toward transparent solar cells for windows and walls, clean hydrogen energy and plant-based bioplastics.
The Japanese government has recently made firm commitments to sustainability, including to contributing zero plastic waste to oceans, and carbon neutrality by 2050.
The country is already a leader in bioplastics and hydrogen energy, and in 2009, it was a Japanese university research team that found that certain crystalline minerals called perovskites are photovoltaic, converting light into a voltage, opening the door to new types of transparent solar cells (pictured below).
Perovskite-based solar cells printed on glass windows, the area of which can exceed roof space in built-up areas, could soon be turning sunlight into energy at efficiencies close to silicon cells. © Panasonic
Commercial solar technology today centres around silicon photovoltaic (PV) cells on rooftops. But while silicon PV has many positive attributes, the solid, opaque layers of silicon the cells require restricts their use on transparent surfaces such as windows, explains Yukihiro Kaneko, who is head of Panasonic Group’s perovskite PV efforts in Osaka, Japan.
Perovskites are formed by ink-like materials that are able to be finely printed on glass, sometimes as transparent or tinted composites. On high rise structures, a building’s vertical plane, often composed of windows, can far exceed the area available on rooftops for solar light capture. If perovskite cells can be incorporated into windows and walls, it could dramatically increase the energy that urban areas can generate, says Kaneko.
For Japan to achieve its decarbonization goals using today’s silicon PVs, he says it would need to build more than 1,300 sports-field-sized solar projects each year. “Building solar cells into windows and walls should dramatically reduce the sprawl of solar farms.”
Since 2009, the development of perovskite materials for efficient energy conversion has advanced in leaps and bounds. A recent report by the German Mechanical Engineering Industry Association predicted that perovskites will be used in commercial solar cells by 2025.
At the forefront of this commercial development are the likes of Oxford PV, a company founded by a physics professor from the University of Oxford, in the United Kingdom, and separately, Panasonic, who, in 2020, produced a large 804cm² perovskite and glass cell at world-leading efficiencies.
While the Oxford PV group are making headway by adding layers of perovskite to silicon-based solar cells to enhance efficiencies by roughly 30%, some of the limitations of the older silicon technology persist in this reformulation.
Panasonic, on the other hand, are taking their expertise in inkjet printing and perovskite photovoltaic materials to create some of the world’s most efficient perovskite and glass solar cells. By optimizing crystal growth and thickness uniformity when coating glass with perovskites, Panasonic are working toward matching the efficiencies of today’s silicon PVs, but with the benefits of flexible and transparent designs.
The question is — how close are we? In academic research, perovskite solar cells have been reported with solar energy conversion efficiencies of more than 26%, rivalling the best silicon solar cells. However, these records are typically achieved on research-scale solar cells 1 cm² or less.
Yukimune Kani’s team develops layered double hydroxides as electrocatalysts with high activity for oxygen evolution; the latest has particles of less than 10 nm. On the left is an anode for an alkaline electrolyzer, on the right is a membrane electrode assembly for an anion exchange membrane electrolyzer. © Panasonic
Panasonic are focused on producing very large-scale perovskite solar cells, says Kaneko. “Generally speaking, the efficiency of a solar cell will decrease as the size increases. Our 804cm2 cells’ 17.9% efficiency was the world record for a perovskite solar cell of that size in 2020 according to charts maintained by the US National Renewable Energy Lab.” Next, the company is transitioning to metre-scale cells.
Another advantage of perovskite solar technologies is they only require processing temperatures of 100°C to 200°C, which is more energy efficient than current technologies, Kaneko points out. In contrast, the process for producing high purity silicon for solar cells from quartzite happens at more than 1,000°C.
The ability to print the cells brings further benefits. “Inkjet printing will enable us to print to any size,” Kaneko says. For the applications the company envisions, that flexibility is important. “Windows and walls come in a wide variety of sizes,” he says. By laser scribing after printing, the company can make perovskite films that are transparent or tinted for windows, or opaque for walls.
But for real-world applications, the challenge is improving the working lifetime of perovskite cells, says Kaneko. Perovskites are particularly vulnerable to moisture. Panasonic’s strategy is to inkjet print perovskites on to glass, then add a second glass sheet to encapsulate the perovskite between two moisture-impermeable layers. The company has also introduced perovskite ink formulation modifications, such as the use of rubidium or caesium additives, to improve the thermal stability of the cell (Ref.1).
Kaneko hopes to have large-scale demonstration materials ready in 2025, and to reach the market within five years.
Transitions to energy systems that produce less CO2 will require clean energy storage, in the case of solar, for example, to capture excess electricity produced during peak sunlight periods for release during low-light periods.
One promising approach is to use renewables to drive electrolysis to split water molecules into hydrogen and oxygen. This ‘green hydrogen’ has many potential uses, including converting stored energy into electricity to power fuel cells and replacing hydrogen produced using fossil fuels, such as natural gas. Oil refineries, and ammonia and methanol production, for example, use hydrogen produced using fossil fuels, so a transition to green hydrogen could significantly reduce CO2 emissions.
“Panasonic develops perovskite PV, batteries and fuel cells — so it was obvious that we should develop green hydrogen production tech to fill in that missing part,” says Yukimune Kani, who leads Panasonic’s water electrolysis effort.
Rare materials are often used as electrocatalysts, adds Kani, but there is a risk of shortages. Since 2018, Kani’s team has developed anode electrocatalysts with high electrocatalytic activity free of precious metals. After intensive exploration of candidate materials, the team selected materials called layered double hydroxides, made from abundant and inexpensive nickel and iron.
The team recently developed what they believe is a world-first method of making a layered double hydroxide with a particle size of less than 10 nm (Ref. 2). “The high activity of our material is derived from the increased surface area that we achieved by miniaturization of the particle sizes,” Kani explains. It’s also created using a low temperature process, which adds to its sustainable CO2 production profile. Panasonic’s layered double hydroxide electrocatalyst can be applied to both alkaline and anion exchange membrane water electrolysis.
Testing the durability of this nanoparticle electrocatalyst is now underway. “By 2025, we hope to supply samples to electrolyser manufacturers for testing,” says Kani. “Water splitting is a very active and competitive area of research, so we need to accelerate our development.”
A plant-derived cellulose fibre resin composite called ‘kinari’ (left) is being used to make products ranging from simple containers (right) to the complex chassis of cordless stick vacuum cleaners. © Panasonic
In 2019, Japan, which is the world’s second largest plastics consumer, committed to stop adding any more plastic waste to the ocean by 2050. Another Panasonic-developed eco-material — a plant-based replacement for conventional fossil fuel-derived plastics — is designed to help Japan address this issue.
The cellulose fibre resin composite ‘kinari’ has already hit the market in products ranging from buttons for sustainable clothing, to the chassis of cordless stick vacuum cleaners. Able to form strong and mouldable composites, the cellulose fibres are also biodegradable via composting and can be recycled a number of times without degradation of performance.
“We are making the process more sustainable, by using cellulose from waste streams such as coffee grounds”
The first challenge when developing the new product was to innovate a new cellulose production process, says Toshifumi Nagino, who is head of Panasonic’s cellulose products efforts. Conventional methods for extracting cellulose from wood pulp are energy intensive, he explains. The cellulose fibres must be separated into individual strands, which is traditionally done using water treatment. Drying these requires a lot of energy, generating 2.3 kg of carbon emissions per kilogram of cellulose fibre.
Nagino and his team eliminated the need for drying by separating and dispersing the cellulose fibres in molten resin instead. The process produces just 0.5 kg of carbon emissions per kilogram of cellulose fibre. This cellulose fibre composite resin pellet can be directly blended with other resins, prior to product moulding.
The final molded composite material contains at least 55% cellulose, and the team have also released materials containing 70% cellulose. Formulations of up to 85% cellulose are in development.
In addition, Panasonic has developed a plastic waste sorting technology, based on near-infrared analysis, to identify and separate different types of plastic in the recycling stream. Cellulose produces a strong characteristic peak under infrared analysis, which can be used to easily identify the cellulose composite material for recycling.
The robust cellulose fibres can readily withstand more than one round of recycling, the team has shown. “The cellulose fibre is very strong, and the cellulose composite does not lose its strength even after repeated reprocessing,” Nagino says. Glass fibre reinforced composites, in contrast, lose their mechanical strength after a single round of recycling, he points out.
Multiple projects are ongoing to expand the cellulose fibre composite line. “We are developing processes and equipment to improve productivity, so that we can make this bioplastic at the same cost as common resins,” says Nagino.
“We are also making the process even more sustainable, by developing the means to use cellulose from various waste streams such as coffee grounds, as well as wood from forest thinning and from bamboo.” Composites for large appliances and automotive parts are also in the pipeline, as are marine biodegradable variants.
The key to reaching Japan’s sustainability goals is turning research into real-world results, says Kaneko. With ambitious commitments and the year 2050 looming, Japan can’t ignore that more sustainable products need to be on the market in the near future, he says.
References
1. Matsui, T. et al. Adv. Mater. 31, 1806823 (2019)
https://onlinelibrary.wiley.com/doi/epdf/10.1002/adma.201806823
2. Koshikawa, H. et al. ACS Catal. 10, 1886 (2020).
https://pubs.acs.org/doi/10.1021/acscatal.9b04505
The texts contents of this article were originally produced in partnership with Nature Portfolio as an advertisement feature and published on 1 September 2023 in the online version of Nature (nature.com), a weekly international journal publishing the finest peer-reviewed research in science and technology. The advertisement feature can be found here: Three sustainable Japanese technologies to watch (nature.com). The advertisement feature will also be running in 23 November 2023 issue of Nature as part of an advertisement feature supplement.
The content in this website is accurate at the time of publication but may be subject to change without notice.
Please note therefore that these documents may not always contain the most up-to-date information.
Please note that German, French and Chinese versions are machine translations, so the quality and accuracy may vary.