
2024.03.22
Panasonic Group People
Applying “Karakuri” from the Edo Period to Enhance
Manufacturing Site Efficiency: Hiroshige Tokuyoshi
Series:
Unlocking 
with User-Friendly
*Japanese only
Master of Karakuri-based Worksite Improvement
Hiroshige Tokuyoshi
Production Engineering Business Unit, Manufacturing Innovation Center,
Lighting Business Division, Electric Works Company, Panasonic Corporation
Joined the company in 1992. Initially assigned to the Niigata Factory, where he was a manufacturing operator in charge of equipment maintenance and process quality control. He then worked for eight years on introducing the fill-up production system* and SCM reform. Today, he is in charge of worksite improvement at factories. Valuing both a comprehensive perspective and a mindset of ensuring the customer comes first cultivated through various experiences, he continues to pursue improvements from new angles to make life easier for those at the manufacturing site.
*A production system based not on prediction but on actual sales information
Reducing on-site work loss and stress with
karakuri-based worksite improvements

I have been promoting worksite improvements at the plant with karakuri mechanisms (karakuri are traditional Japanese mechanized puppets; the word has also come to mean “mechanisms” in Japanese) since 2017. This karakuri-based worksite improvement uses simple apparatuses and mechanisms, like the mechanized puppets of the Edo period, to improve work efficiency at low cost without using electricity, air, or other power sources. While placing importance on the concept of making someone’s life easier quickly, I work across operating companies to solve worksite problems. At the same time, I help support human resource development through courses and training.
As one of the model smart factories, the Niigata Factory has actively adopted advanced technologies such as IoT, AI, and robots to promote automation and build a smart production system. The automation of manufacturing provides many benefits. On the other hand, it also has drawbacks, such as people needing to adapt to the machines. As more and more work requires addressing malfunctions and making complex judgments, it can become a source of stress and create a new burden on those at the worksite. These problems require some kind of improvement that will address the concerns of and issues faced by those at the worksite. That’s why I decided to learn from scratch how to improve the worksite with karakuri mechanisms and introduce those improvements. The impetus for that came from the site manager, who said, “Managing high-tech equipment takes so much labor that I don’t know whether we’re making things or maintaining equipment. I want to create an environment where those at the manufacturing site can concentrate more on manufacturing.” However, with the plant as a whole moving toward smarter systems, it was hard to gain understanding for the use of karakuri, which are analog mechanisms... I had to start learning whenever I had time.
Success requires the ability to persevere
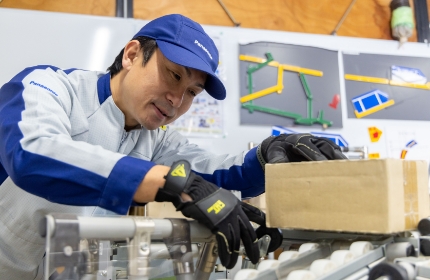
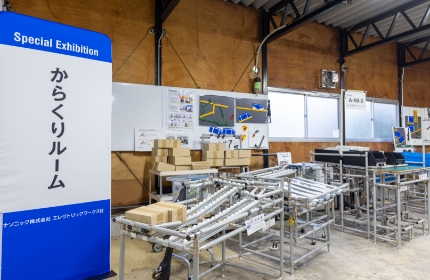
At the time, I was in charge of installing state-of-the-art equipment, so I was actually a karakuri nay-sayer myself (laughing). I kept asking myself if there was really any point in doing it, but my personal policy is that if I start something, I see it through. I hate to lose, and I wasn’t about to compromise. The first device I came up with was one to temporarily stock products to allow for more time to work. The words of gratitude I received from the sites where it was introduced also encouraged me to keep going. I kept coming up with ideas without giving up, and in 2020, I won several awards, including the Commendation for Science and Technology by the Minister of Education, Culture, Sports, Science and Technology (The Award for Creativity). Gradually, the practicality and effectiveness of the mechanisms were recognized, and I began to receive orders for equipment and requests for courses and training from both inside and outside the company.
What I got a strong sense of through this challenge was the importance of giving things a try without judging them based on whether it’s something you enjoy or can do. Give it a try, and don’t be afraid to fail. In this day and age, you can look anything up, and if you don’t understand something, all you have to do is ask someone. I added the new option of karakuri, or semi-automation, to the dichotomy of full automation or manual labor. This expanded the variety of on-site work. There are many interesting things to do and learn that you only discover when you give things a try. I am convinced that the path to success is to take that courageous first step without getting caught up in the reactions of those around you or stereotypes.
Going forward, I hope to broaden the scope of karakuri-based worksite improvement and establish an environment where anyone can take up the challenge. I would also like to establish rules within the Panasonic Group so we can continue to make improvements that make life easier for people at the manufacturing site. By improving the environment, I want people working at the manufacturing site to grow fonder of the company. That’s my biggest desire. I hope to promote the appeal of karakuri mechanisms, which are safe and easy for anyone to use and connect workers and machines, both internally and externally.
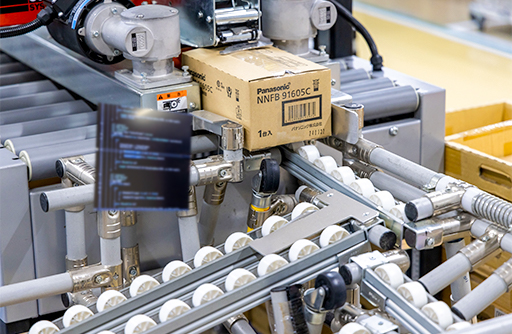
Karakuri device No. 1, the first to be introduced at a worksite. All of the materials used were purchased at a home improvement store. The cost of making it was about 46,000 yen. It took five days.
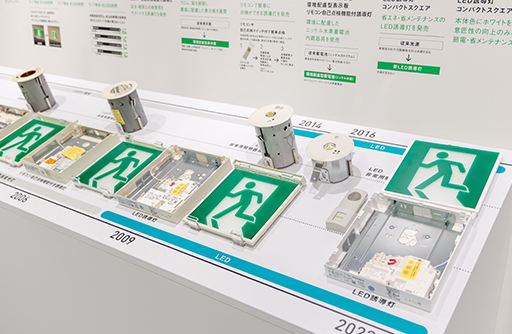
The Niigata Factory, which opened in 1973, mainly manufactures lighting fixtures for office ceilings and disaster prevention lighting, such as emergency lights and illuminated emergency exit signs.
The content in this website is accurate at the time of publication but may be subject to change without notice.
Please note therefore that these documents may not always contain the most up-to-date information.
Please note that German, French and Chinese versions are machine translations, so the quality and accuracy may vary.