
2024.03.22
Panasonic Group People
Paving the Way for the Dry Battery Business
with Manufacturing for a New Era: Toma Suzuki
Series:
Unlocking the
: Stepping Out of the Comfort Zone to Eusure the Best Life for Employees
*Japanese only
A young leader taking up the challenge of factory logistics reform
Toma Suzuki
Production Engineering Dept., Manufacturing Management, Consumer Energy Business Unit
Energy Device Business Division, Panasonic Energy Co., Ltd.
Joined the company in 2016. He was initially involved in maintaining, designing, and developing production equipment at the Moriguchi Factory, which produces dry batteries. In 2020, he was transferred to the Global Manufacturing Promotion Department to work on the introduction of new equipment at overseas production bases, including Thailand. He has been in his current position since 2022. He continues to pursue a manufacturing system that will pave the way for the dry battery business.
Smart production system incorporating
automated transfer
based on worksite feedback
The project to end production at the Moriguchi Factory (Moriguchi City, Osaka), which has met domestic demand for dry batteries for over 90 years, and transfer production to the Nishikinohama Factory (Kaizuka City, Osaka) began in 2020. I was one of the key participants in that project. The distance products were being transported within the premises increased as the site area grew, so we introduced new manufacturing mechanisms such as the automated transfer system and automated warehousing system to shorten lead times, reduce inventories, and save labor.

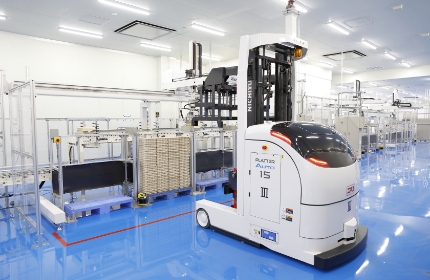
Introducing an automated transfer system to such a large factory was also a big challenge for the company. I volunteered to be in charge and began by learning the basics, including seeking guidance from infrastructure-related manufacturers to acquire the necessary knowledge. Some at the worksite were less than enthusiastic and expressed reservations about the introduction of the automated transfer system. After sitting down with them, however, it turned out that most were not opposed to the change. They were just concerned about the system’s complex operating procedures and the impact on operations. I believed it was important to ensure optimal communication by listening to all feedback and understanding people’s thoughts, so I visited the factory of the equipment manufacturer together with employees from the worksite early on. I had them experience the automated transfer system firsthand so they could get a picture of what it would look like in completed form at the Nishikinohama Factory. Gradually, the increased understanding brought them on board with the plan. In addition, the transport distances were short at the Moriguchi Factory, so there was less opportunity for wasted effort or issues to surface. As such, I took the opportunity to work closely with employees on the front lines and survey them to see if there were any undue burdens or unnecessary tasks. By visualizing the issues, the entire factory is now facing fundamental issues in the production system that had previously been overlooked.
The basis of these efforts is a concept I learned from a senior colleague when I first joined the company, namely that for those of us who design and develop equipment to increase productivity, our customers are the employees at the manufacturing site. For example, I believe that even though these are colleagues within the Panasonic Group, we can make better things if we treat them like customers. I always tried to think from the customer’s point of view and gather as many opinions as possible, even if it was about something trivial.
Making things easier at the worksite:
Acquiring knowledge to tackle automation
The project was completed after about three years, and full-scale operation was launched at the Nishikinohama Factory in November 2023. What I became keenly aware of through this challenge was that focusing solely on equipment is not enough in manufacturing. To truly determine the necessary production capacity, you have to understand the big picture of the supply chain, including inventory management and logistics. I also learned that you have to acquire knowledge from a broader perspective to realize whole plant automation. This includes designing pathways for smooth movement between different buildings for automated conveyance. Each time, I communicated with the department in charge and did my own research as we went, but there was a lot of trial and error, so I was always wondering if I was doing the right thing. However, even if something doesn’t go well, you need to look at the positives, such as that you figured out what doesn’t work. Even failure can be a valuable asset. When you take on new and challenging things, it’s only natural that you run into obstacles and difficulties. I try to enjoy the process of searching for answers while thinking about what I lack and what I need to make up for on a daily basis.

The Nishikinohama Factory sought to build a smart production system that does not depend on human labor and has achieved over 80% automation. On the other hand, new challenges have emerged as we have acquired knowledge and perspectives from various fields. In the future, in addition to reducing manufacturing site workloads, I will continue pursuing the creation of an environment that allows us to challenge ourselves to do more creative work so I can help employees involved in the manufacturing of dry batteries live their best.
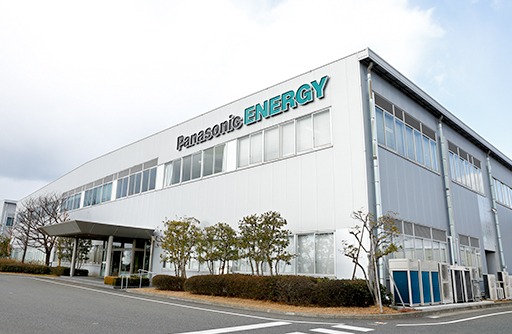
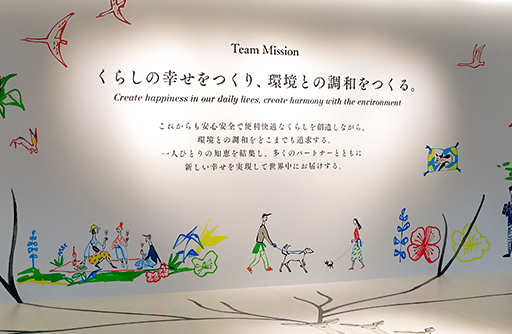
The Nishikinohama Factory is a global flagship factory that will pave the way for the dry battery business. Not only have we built a smart production system incorporating automated transfer, but we have also achieved net zero CO2 emissions by maximizing the use of renewable energy. We also received the Minister of Economy, Trade and Industry Award at the 2023 New Energy Awards for our efforts to introduce solar power generation. Moreover, through activities such as factory tours and battery workshops on making dry batteries by hand for elementary school students, we will continue to evolve to create an attractive factory that is open to the community and society.
The content in this website is accurate at the time of publication but may be subject to change without notice.
Please note therefore that these documents may not always contain the most up-to-date information.
Please note that German, French and Chinese versions are machine translations, so the quality and accuracy may vary.