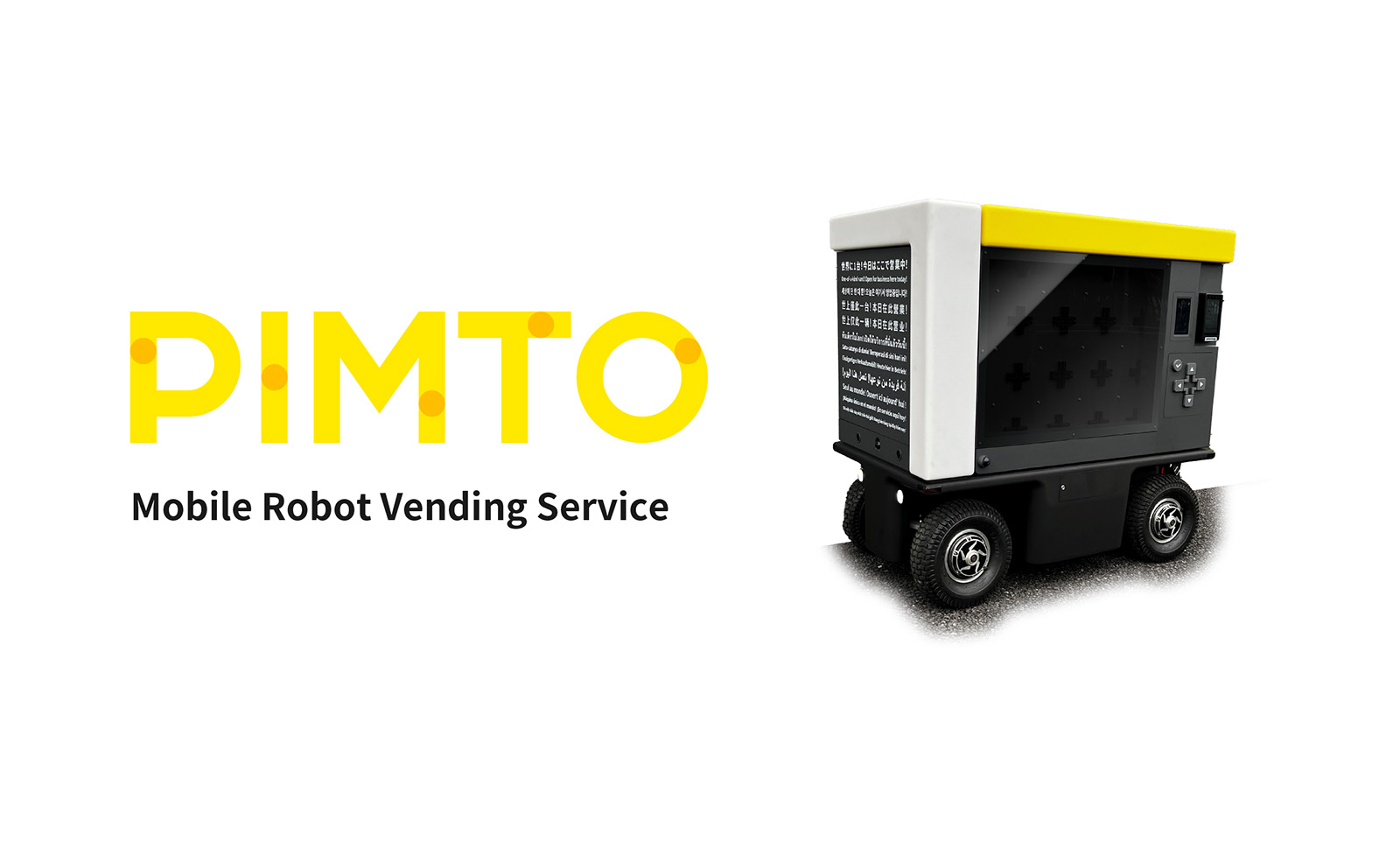
Oct 29, 2024
- Products & Solutions
- Press Release
- Business Solution
- Automotives & Mobility
- Corporate Social Responsibility (CSR)
Mar 27, 2017
Products & Solutions / Press Release
Panasonic's new vehicular high-precision angle sensor is small and light and is capable of detecting rotation angles with high precision. It allows accurate reading of the movements of vehicular motors, giving precise control.
Osaka, Japan - Panasonic Corporation announced today that it has developed an angle sensor called "A³MR" [1] that precisely detects the rotation angle of vehicular motors. This is a small and highly accurate sensor with built-in AMR thin films [2] and Hall elements [3]. The AMR thin films respond to a wide range of strong magnetic fields and the Hall elements are able to detect angles of up to 360°. The sensor meets the requirements of ISO 26262 (functional safety requirements) [4] for sensors incorporated into vehicles.
This newly-developed sensor reads the angle of rotation (rotational angle) of the rotor in the motor to a high degree of precision. This enables accurate detection of the motor's movement, allowing efficient control of the motor's rotational speed and driving amount to achieve more efficient control. The sensor is small and light and is capable of precise detection even in irregular magnetic fields. This characteristic allows side shaft detection [5], which greatly increases the options for sensor attachment. In an Advanced Driver Assistance System (ADAS) [6], for example, the rotation of the power steering or operation of the gearshift exerts control over the behavior of the vehicle through changes in the rotational angle of the motor. Controlling the motor in such a highly precise manner causes the vehicle to travel with precision and puts the driving motor included in an ISG hybrid system [7] under close control. This prevents the motor from running erratically, thus achieving lower fuel consumption by improving its efficiency.
A resolver [8], which is the type of rotation angle sensor currently in widest use, is capable of highly precise detection. It is, however, large and heavy and therefore poses a problem in that redundant design [9], which is required by ISO 26262, is difficult to achieve. Magnetic sensors like GMRs [10] are also in use today. They are relatively compact, but are inferior to the resolver in precision of angle detection. GMRs have another drawback in that they lose their angle detection precision in environments influenced by strong magnetic fields. This has led to market demand for a small and high-precision sensor to replace resolvers and which can be used in a wide range of magnetic field strengths.
Detecting the rotating angle of a vehicular motor (for power steering, ISG hybrid systems, shift-by-wire transmissions [11], etc.)
Samples are scheduled to be shipped out in May 2017. Receipt of product orders will be started in September 2019.
The resolver type, which is capable of high-precision detection, uses bulky coils, posing a problem in that it is large and heavy. AMR thin films can detect the direction of a magnetic field precisely but cannot determine its polarity (positive or negative direction). It therefore detects rotation angles of up to 180°, which is why AMR thin film is not adopted in vehicular motors that require detection of angles of up to 360°. We have now developed a new control circuit by combining AMR thin films with Hall elements, which are capable of determining polarity. We have thus created a sensor that is small and light (1/2 or less in weight of the resolver type) and which detects rotation angles of up to 360° with high precision, paving the way for the use of this type of sensor in vehicular motors.
A magnetic sensor works most effectively in a uniform magnetic field. The sensor, therefore, must be positioned in the small area on the rotating shaft of the motor where the magnetic field is stable. This configuration is, however, not easy because of numerous restrictions created by the design specifications of the motor shaft. The AMR thin film in the developed sensor can detect the direction of a magnetic field precisely, even if its strength is high, eliminating the need to locate the sensor on the motor's rotating shaft. This allows high-precision angle detection at a distance from the motor shaft, where the magnetic field is not uniform, thus increasing the options for system design.
All electric motors generate magnetic fields. A motor sensor needs to work in a strong magnetic field. Conventional sensors, however, tend not to function reliably in strong magnetic fields exceeding 100 mT. The developed sensor maintains its high-precision detection capability in strong magnetic fields of up to 200 mT, and offers superior noise resistance.
It is essential for precise detection of a rotation angle to form a magnetic thin film on which magnetic domains [12] are aligned with the magnetic field generated by the rotating motor. We have developed an AMR thin film whose magnetic domains are readily aligned, through processing and thin-film deposition techniques originally developed by our company. The AMR thin film prevents its magnetic domains from becoming scrambled, enabling very precise detection of the direction of the magnetic field.
The developed sensor includes a control circuit original to our company, which is composed of the AMR element capable of precisely detecting angles of up to 180° plus Hall elements capable of determining polarity, and is therefore able to detect rotation angles of up to 360°. Making good use of the knowledge accumulated during the AMR element development process, we have also achieved a self-diagnostic function, which identifies any state in which the AMR element is likely to fail and immediately warns the electronic control unit of signs of failure. The product has been developed in conformity to ISO 26262 and is compatible with systems that have a hazard category of ASIL-D [13].
Item | Details |
---|---|
Angle detection precision | < ± 0.5° over the whole temperature range |
< ± 0.1° at 25°C after calibration | |
Detected magnetic field area | > 20 mT |
Applied voltage | 4.0 - 5.5 V |
Current consumption | < 15 mA |
Output interface | SPI,SENT |
Panasonic Corporation is a worldwide leader in the development of diverse electronics technologies and solutions for customers in the consumer electronics, housing, automotive, enterprise solutions and device industries. Since its founding in 1918, the company has expanded globally and now operates 474 subsidiaries and 94 associated companies worldwide, recording consolidated net sales of 7.553 trillion yen for the year ended March 31, 2016. Committed to pursuing new value through innovation across divisional lines, the company uses its technologies to create a better life and a better world for its customers. To learn more about Panasonic:
http://www.panasonic.com/global
Panasonic Corporation
Tel: +81-(0)3-3574-5664 Fax: +81-(0)3-3574-5699
The content in this website is accurate at the time of publication but may be subject to change without notice.
Please note therefore that these documents may not always contain the most up-to-date information.
Please note that German, French and Chinese versions are machine translations, so the quality and accuracy may vary.