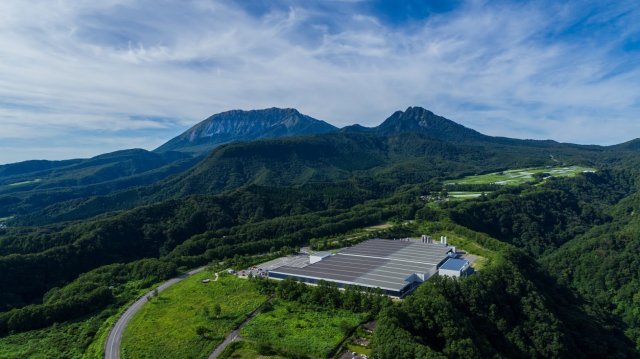
"Suntory Tennensui" is one of the top mineral water brands in Japan. At the end of 2018, one of its water plants, the "Suntory Okudaisen Bunanomori Water Plant" located in Tottori Prefecture became the first plant in Japan to be certified by the international standard, Alliance for Water Stewardship (AWS), in recognition for its contribution to the sustainable use of water in and around the water plant. To become AWS certified, Panasonic's proprietary know-how was adopted to improve the wastewater treatment facility. In recent years, environmental awareness has amplified, and the sustainable use of precious water resources is becoming increasingly important. This article introduces the commitment of the Suntory Group and Panasonic Environmental Systems & Engineering to environmental conservation.
Summary
- In 2018, "Suntory Okudaisen Bunanomori Water Plant" became certified by AWS, international standard for "sustainable water management."
- Its contribution to the sustainable use of water in and around the water plant was globally recognized.
- Panasonic's environmental engineering and technical capabilities helped Suntory satisfy strict water quality standards.
- Pure water production technology was applied to a wastewater treatment facility.
Water is fundamental--Suntory Group's unwavering water philosophy
Suntory Group, whose mission is "to create harmony with people and nature," has a reputation for being a company with high level of environmental awareness. At its core lies the concept of "giving back to society" that has been cherished since the company was founded in 1899. This means mainly three things--to reinvest profits, provide services to customers and partners, and contribute to society. As this history represents, social contribution has been a part of Suntory's DNA since its foundation.
After the Sustainable Development Goals were established by the United Nations in 2015, Suntory Group has reinforced its focus on sustainability. In July 2019, Suntory Group formulated its "Sustainability Vision." It identified seven important themes--water, CO2, raw ingredients, containers and packaging, health, human rights, and enriching life--to help realize a society where people live in harmony with nature.
Water is particularly important to the Suntory Group. Its attitude towards water is summarized in its "Sustainable Water Philosophy" drafted in January 2017. The Sustainable Water Philosophy shared by its group companies is comprised of four parts, 1. Understanding the natural cycle of water, 2. Promoting environmentally conscious water use, 3. Conserving watersheds, and 4. Engaging with the local community. Not only does it save water during its business activities, and practices sophisticated water recycling, in 2003, it launched water conservation activities named Tennensui No Mori (Natural Water Forest) to protect nature's rich water resources. There are 21 Tennensui No Mori in Japan, in 2019, it achieved its target--to recharge two times the amount of groundwater its factories use across Japan.
The brand of mineral water it introduced in 1991, "Suntory Tennensui," embodies this Sustainable Water Philosophy. This brand has made great strides since then; in 2018 the Suntory Tennensui became the top selling beverage in the domestic soft drink market. And the brand has grown to become a core product for the group.
Suntory Tennensui is currently being bottled in three factories, one of which is the Suntory Okudaisen Bunanomori Water Plant in Kofu Town, Hino County, Tottori Prefecture (hereafter referred to as the Okudaisen Factory). Okudaisen Factory lies at the heart of the Daisen mountain, a renowned mountain in Tottori Prefecture. It is a scenic location surrounded by nature. That is why ever since the factory began operating in 2008, it has paid respect to its surrounding environment. These efforts have been well recognized, with the factory being given numerous awards including the Ministry of Economy, Trade and Industry's "100 New Energy" and "Technology Award" from the Japanese Society of Revegetation Technology.
In December 2018, the factory acquired the first Alliance for Water Stewardship (AWS) certification in Japan. AWS is an organization that promotes a universal framework for the "sustainable use of water." It is comprised of NGOs such as the World Wildlife Fund (WWF), investor group CDP, and non-alcoholic and alcoholic beverage companies. The AWS Standard evaluates factories around the world for their sustainable use of water, and Okudaisen Factory was hailed for its water conservation and stewardship efforts. In short, it has been globally recognized as a "factory that is in harmony with nature and the region."
A more sophisticated wastewater treatment facility was necessary to launch a new range of products
Okudaisen Factory has focused on production of Suntory Tennensui by utilizing precious water resources. In 2017, another line was added to manufacture carbonated beverages such as the "Suntory Okudaisen Sparkling" and flavored water such as the "Yogurina & Suntory Tennensui" and "Asa-zumi Orange & Suntory Tennensui."
With the launch of flavored water, the Okudaisen Factory added a wastewater treatment facility for the new line. Suntory chose Panasonic Environmental Systems & Engineering to provide the solution. Masataka Kusumi of Suntory Products explained how this collaboration came about.
"At the Okudaisen Factory we used to only bottle Suntory Tennensui, so our facility was in compliance with standards for mineral water wastewater treatment. However, the new line for flavored water will deal with other substances as well, so we had to install equipment that could handle more intense water treatment. With the existent facility we could not meet the wastewater standards that is in line with our policy. That is why we reached out to Panasonic and they proposed to combine an RO treatment facility to meet our benchmark."
Masataka Kusumi
Section Manager
Engineering Section
Okudaisen Bunanomori Water Plant
Suntory Products Ltd.
RO treatment is a pure water treatment technology that extracts nearly pure water molecules by using reverse osmosis membranes. It is most often applied to potable water, foods, and semiconductor manufacturing. Mr. Kusumi also stated that "it's quite unique to utilize this technology for wastewater treatment." The wastewater is biologically treated, then purified by reverse osmosis until it is as clean as tap water before being discharged. The Okudaisen Factory goes to this extent to clean its wastewater because the water is discharged into the Hosotani River that flows nearby the factory.
Suntory has adopted technology that utilizes RO membranes to discharge clean water into the Hosotani River.
Mr. Kusumi added, "At the Okudaisen Factory, we manage wastewater by voluntarily applying standards that are more strict than the Water Pollution Prevention Act and the environmental preservation agreement with the Kofu Town. Thanks to Panasonic's solution, we can turn murky wastewater transparent, and the quality of the water discharged is on par with natural water. I have experienced the operation and management of wastewater treatment facilities at various factories in the past, but this solution gives me great confidence. It really doesn't require hands-on management."
Hiroshi Naito of Suntory Holdings played a key role in acquiring the AWS certification.
"From 2003, as part of our Tennensui No Mori efforts, we have been managing forests. We have continued to undertake these activities whilst focusing on the importance of water resources and effectiveness, and now this has transformed into our strength.
"From this perspective, AWS's philosophy and Suntory Group's Sustainable Water Philosophy is very similar. However, after the enactment of the SDGs, a more global environmental approach became necessary, so it was no longer enough to gauge our efforts simply based on domestic standards. I applied for the AWS certification because I wanted Suntory Group's efforts to be evaluated based on global standards.
"The Okudaisen Factory was the optimal place to apply for AWS certification. There were exacting management standards in place, and from the moment we broke ground, we were working in close concert with the local community. And because the area is situated nearby a national park, the people of this region had a high awareness for 'clean water' from before. And the timing was also opportune because we had just installed a RO treatment based sophisticated wastewater treatment facility," explained Mr. Naito.
Hiroshi Naito
Senior General Manager
Corporate Sustainability Department
Corporate Sustainability Division
Suntory Holdings Limited
Once a year, the Okudaisen Factory organizes a monitoring committee comprised of representatives from the local government, experts, and local residents. The acquisition of the AWS certification was well received by the committee. Applying the learnings from Okudaisen, "Suntory Kyushu Kumamoto Plant" became the second factory in Japan to obtain the AWS certification in December 2019.
"We became the first company to obtain the AWS certification for two of our factories, but we hope that many others will follow suit. People tend to take water for granted. But because it is tasteless and odorless, and transparent, it needs to be meticulously managed. We hope to continue to deliver nature's blessing in pristine condition to our customers," added Mr. Naito.
A new challenge produced great results
The wastewater treatment facility delivered by Panasonic Environmental Systems & Engineering can process 370 tons of wastewater a day. As mentioned earlier, RO treatment purifies the discharge to levels on par with rainwater or tap water, and by combining RO membranes and vacuum concentration, Suntory Group has successfully reduced waste materials to 1/150 of former levels.
Moreover, at the beginning of the wastewater treatment facility you will find six tanks. Suntory and Panasonic met numerous times before installation to discuss the discharge conditions, meticulously ran multiple simulations to propose ways to make the wastewater treatment facility efficient. The proposal also contributed to reducing facility costs.
Six tanks for storing wastewater from the factory. They store wastewater to make the amount of wastewater treated constant and to homogenize the concentration of the wastewater to stabilize processing.
Tomoaki Okuda of Panasonic Environmental Systems & Engineering, who was in charge of installation, explained, "We were first approached back in August 2015. We defined the requirements for discharge and began working onsite from June 2016."
Tomoaki Okuda
Senior Coordinator
Plant Engineering Unit
Environmental Solutions Business Group
Panasonic Environmental Systems & Engineering Co., Ltd.
Paying the utmost respect to the surrounding environment and purifying the discharge to as close to the original natural state as possible--this task was a new challenge for Panasonic Environmental Systems & Engineering as well. The water quality standards demanded of the Okudaisen Factory included expected criteria such as BOD (Biochemical Oxygen Demand) and COD (Chemical Oxygen Demand) as well as the electrical conductance of the liquid. Purer the water, lower the conductivity.
According to Mr. Okuda, "To meet these standards, we applied RO treatment, which isn't usually applied to wastewater. RO membranes guarantee a certain level of conductivity to ensure that the Okudaisen Factory water quality standards are fulfilled before ultimately being discharged. Waste produced during this process is treated using RO membranes and an evaporative concentration device, but there were concerns that the silica in the water would clog the membranes or the evaporative concentration device may not operate stably. One of Panasonic's departments that specializes in chemicals provided input to prevent scaling.
"Until now, I was mainly in charge of wastewater treatment, so it was the first time I implemented an RO membrane unit for making pure water. The diversity of our know-how enabled us to meet our customer's needs and to answer the challenge. Working together with the people of the Okudaisen Factory, we were involved until we ran the water and conducted a test run. We learned quite a lot from this project."
Seigou Watanabe from Panasonic Environmental Systems & Engineering, who was involved in this project as Mr. Okuda's supervisor, described the project as follows: "It was quite challenging. We had never worked on a project that required the discharge water to be so high in quality, but with numerous reiterations and careful consideration we were able to propose the optimal solution."
Mr. Watanabe noted, "Because water treatment did not impact productivity, main focus in the past had been on the reduction of facility costs. But after 2015, 2016, SDGs began to gain momentum, and we have noticed that more clients now perceive commitment to environmental contribution as an added value. We notice that this is the case every day when we talk to our clients. And this project for Suntory made us realize that recycling of resources also adds value."
Mr. Watanabe foresees that society's need for recycling of water and other resources will increase, so he has recommended that this be included in the growth strategy of his Plant Engineering Unit. Today, the business group's mission is "to create a sustainable water future."
Of course, once the facility is installed, it requires regular inspection, maintenance, and management. Due to COVID-19 and the decrease in the working population, demand for systems that can be operated by fewer people is increasing. Bearing this social landscape in mind, Panasonic Environmental Systems & Engineering is drawing on the collective power of the Panasonic Group to develop an automatic monitoring system.
"People are working from home and with labor shortages, more and more companies are asking us to help them with automation and manpower reduction. At the moment, the Panasonic Group is working with a company that specializes in image data processing to develop a system that can automatically monitor the water quality," said Mr. Watanabe.
Main control board that manages the condition of each equipment that make up the wastewater treatment facility.
Mr. Okuda, who has been working on wastewater treatment since joining the firm 17 years ago, added, "My dream is to rid factories of wastewater. I want to develop a system that recycles water in the process of manufacturing, that produces the least amount of waste possible. I hope to hone our technological capabilities so that we can achieve this goal."
Mr. Naito of Suntory Holdings described his hopes for Panasonic's technological capabilities, "Panasonic has solutions that use big data, AI, IoT, and robots to reduce the manpower required at manufacturing sites. If we take advantage of these solutions, we can accelerate our efforts." And Mr. Kusumi of Suntory Products stated, "I hope Panasonic will develop innovatively new technologies and solutions that will enable us to achieve our energy saving, water saving targets."
We use water every day, so we do not give a second thought about its importance. But the story of how the Suntory Tennensui came to being is representative of Suntory Group's commitment to contributing to the environment. And this product, which truly "creates harmony with people and nature," was brought to life by the close collaboration between two major corporations.
# # #
Disclaimer:
We would like to note that Panasonic Newsroom is not a place to address personal Customer Service issues. Even though this is not the forum, Panasonic is always eager to resolve your concerns. Our local customer services contacts can be found at Global Support or you can see our list of Social Media Accounts to find the right channel for your queries and concerns.