
2024.03.22
Personnes du groupe Panasonic
Ouvrir la voie au secteur des batteries sèches
avec Fabrication pour une nouvelle ère : Toma Suzuki
Déverrouillage du
: Sortir de la zone de confort pour offrir la meilleure vie aux employés
*Japonais uniquement
Un jeune leader qui relève le défi de la réforme de la logistique industrielle
Tom Suzuki
Département d'ingénierie de production, gestion de la fabrication, unité commerciale de l'énergie grand public
Division commerciale des appareils énergétiques, Panasonic Energy Co., Ltd.
A rejoint l'entreprise en 2016. Il a d'abord été impliqué dans la maintenance, la conception et le développement des équipements de production à l'usine de Moriguchi, qui produit des piles sèches. En 2020, il a été transféré au département Global Manufacturing Promotion pour travailler sur l’introduction de nouveaux équipements dans les bases de production à l’étranger, notamment en Thaïlande. Il occupe son poste actuel depuis 2022. Il continue de mettre en place un système de fabrication qui ouvrira la voie au secteur des batteries sèches.
Système de production intelligent intégrant
transfert automatisé
basé sur les retours de chantier
Le projet visant à mettre fin à la production de l'usine de Moriguchi (ville de Moriguchi, Osaka), qui répond à la demande intérieure de piles sèches depuis plus de 90 ans, et à transférer la production à l'usine de Nishikinohama (ville de Kaizuka, Osaka), a débuté en 2020. J'étais l'un des les principaux acteurs de ce projet. La distance de transport des produits dans les locaux augmentait à mesure que la superficie du site augmentait. Nous avons donc introduit de nouveaux mécanismes de fabrication tels que le système de transfert automatisé et le système d'entreposage automatisé pour raccourcir les délais de livraison, réduire les stocks et économiser la main d'œuvre.

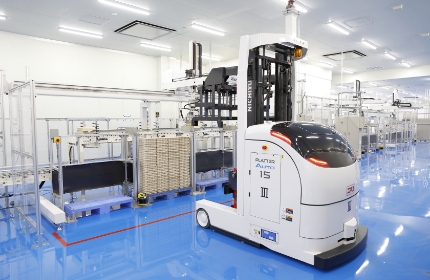
L'introduction d'un système de transfert automatisé dans une usine d'une telle taille représentait également un défi de taille pour l'entreprise. Je me suis porté volontaire pour être responsable et j'ai commencé par apprendre les bases, notamment en demandant conseil auprès de fabricants liés aux infrastructures pour acquérir les connaissances nécessaires. Certains sur le chantier étaient peu enthousiastes et ont exprimé des réserves quant à l'introduction du système de transfert automatisé. Après s’être entretenus avec eux, il s’est toutefois avéré que la plupart n’étaient pas opposés au changement. Ils étaient simplement préoccupés par les procédures opérationnelles complexes du système et par leur impact sur les opérations. J'ai pensé qu'il était important d'assurer une communication optimale en écoutant tous les commentaires et en comprenant les pensées des gens. J'ai donc visité très tôt l'usine du fabricant d'équipements avec les employés du chantier. Je leur ai fait expérimenter le système de transfert automatisé afin qu'ils puissent avoir une idée de ce à quoi il ressemblerait une fois terminé à l'usine de Nishikinohama. Peu à peu, une meilleure compréhension les a amenés à adhérer au plan. De plus, les distances de transport étaient courtes à l'usine de Moriguchi, ce qui réduisait les risques de gaspillage d'efforts ou de problèmes. À ce titre, j’ai profité de l’occasion pour travailler en étroite collaboration avec les employés de première ligne et les sonder pour voir s’il y avait des fardeaux excessifs ou des tâches inutiles. En visualisant les problèmes, l’ensemble de l’usine est désormais confronté à des problèmes fondamentaux du système de production qui avaient été négligés auparavant.
La base de ces efforts est un concept que j'ai appris d'un collègue senior lorsque j'ai rejoint l'entreprise pour la première fois, à savoir que pour ceux d'entre nous qui conçoivent et développent des équipements pour augmenter la productivité, nos clients sont les employés du site de fabrication. Par exemple, je crois que même s'il s'agit de collègues du groupe Panasonic, nous pouvons faire de meilleures choses si nous les traitons comme des clients. J'ai toujours essayé de penser du point de vue du client et de recueillir autant d'avis que possible, même s'il s'agissait de quelque chose de trivial.
Faciliter les choses sur le chantier :
Acquérir des connaissances pour aborder l’automatisation
Le projet a été achevé au bout d'environ trois ans et l'exploitation à grande échelle a été lancée à l'usine de Nishikinohama en novembre 2023. Ce dont j'ai pris conscience grâce à ce défi, c'est que se concentrer uniquement sur l'équipement ne suffit pas dans la fabrication. Pour véritablement déterminer la capacité de production nécessaire, vous devez comprendre l’ensemble de la chaîne d’approvisionnement, y compris la gestion des stocks et la logistique. J'ai également appris qu'il faut acquérir des connaissances dans une perspective plus large pour réaliser l'automatisation de l'ensemble d'une usine. Cela inclut la conception de voies permettant une circulation fluide entre les différents bâtiments pour un transport automatisé. À chaque fois, je communiquais avec le service responsable et faisais mes propres recherches au fur et à mesure, mais il y avait beaucoup d'essais et d'erreurs, donc je me demandais toujours si je faisais la bonne chose. Cependant, même si quelque chose ne se passe pas bien, vous devez examiner les aspects positifs, comme par exemple comprendre ce qui ne fonctionne pas. Même l’échec peut être un atout précieux. Lorsque vous vous lancez dans des activités nouvelles et stimulantes, il est tout à fait naturel que vous rencontriez des obstacles et des difficultés. J'essaie de profiter du processus de recherche de réponses tout en réfléchissant à ce qui me manque et à ce que je dois rattraper au quotidien.

L'usine de Nishikinohama a cherché à construire un système de production intelligent qui ne dépend pas du travail humain et a atteint un taux d'automatisation de plus de 80 %. D’un autre côté, de nouveaux défis sont apparus à mesure que nous avons acquis des connaissances et des perspectives dans divers domaines. À l'avenir, en plus de réduire la charge de travail sur les sites de fabrication, je continuerai à créer un environnement qui nous permette de nous mettre au défi de faire un travail plus créatif afin d'aider les employés impliqués dans la fabrication de piles sèches à vivre de leur mieux.
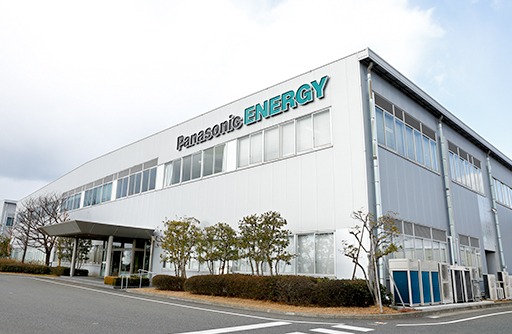
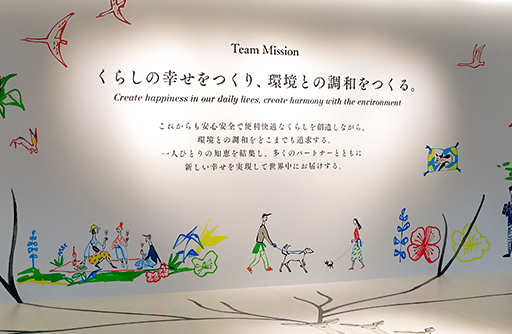
L’usine de Nishikinohama est une usine phare mondiale qui ouvrira la voie au secteur des batteries sèches. Non seulement nous avons construit un système de production intelligent intégrant un transfert automatisé, mais nous avons également atteint zéro émission nette de CO2 en maximisant l'utilisation des énergies renouvelables. Nous avons également reçu le prix du ministre de l'Économie, du Commerce et de l'Industrie lors des New Energy Awards 2023 pour nos efforts visant à introduire la production d'énergie solaire. De plus, grâce à des activités telles que des visites d'usines et des ateliers de fabrication de piles sèches à la main pour les élèves du primaire, nous continuerons d'évoluer pour créer une usine attrayante et ouverte sur la communauté et la société.
Le contenu de ce site Web est exact au moment de la publication mais peut être sujet à changement sans préavis.
Veuillez donc noter que ces documents ne contiennent pas toujours les informations les plus récentes.
Veuillez noter que les versions allemande, française et chinoise sont des traductions automatiques, de sorte que la qualité et la précision peuvent varier.