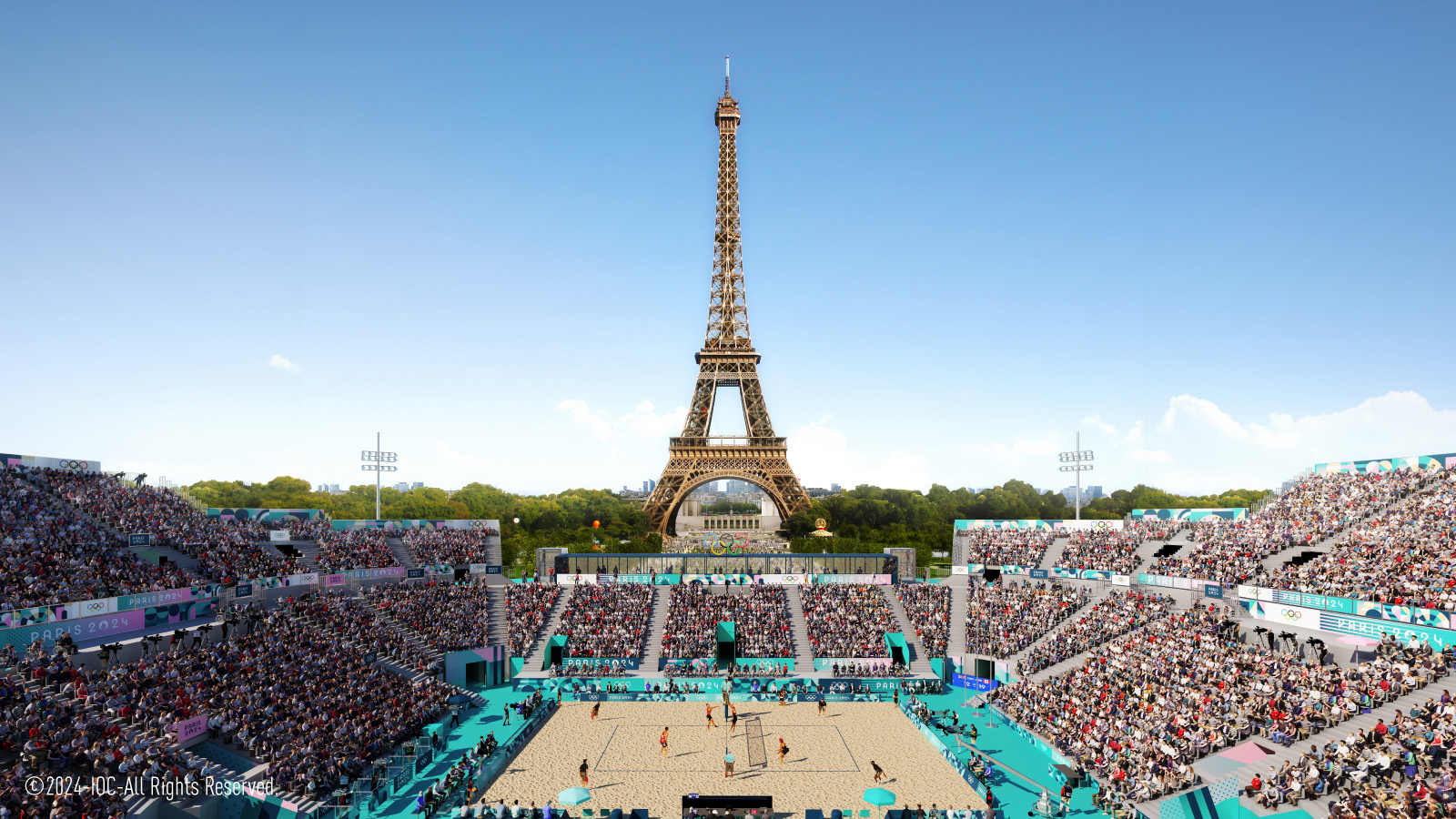
Apr 15, 2024
- Products & Solutions
- Press Release
- Olympics Paralympics
- Europe and CIS
- Business Solution
Feb 28, 2024
Products & Solutions / Press Release
Saves space for capacitor mounting areas, contributing to a reduction in environmental impact through the miniaturization of ECUs and a decrease in the amount of parts and materials used.
Tokyo, Japan – Panasonic Industry Co., Ltd. (Headquarters: Minato-ku, Tokyo; Representative Director, President, CEO: Shinji Sakamoto) announced today that it has begun commercial production of its ZL series conductive polymer hybrid aluminum electrolytic capacitors. The series includes the industry's first high-capacitance type models guaranteed to operate at 135°C. These capacitors have been developed for installation in electronic control units (ECUs)[1] for electric vehicles (now sometimes referred to as xEVs, a catchall for EVs and all their subtypes), including hybrids. Mass production is slated to begin in February 2024.
Conductive polymer hybrid aluminum electrolytic capacitors, characterized by high capacitance and high current, are responsible for reducing current noise and stabilizing circuit voltage in ECU power supply circuits, with more than 100 packs used in a typical xEV. They are key devices that are indispensable for the electrification and advanced digitization of vehicles. In recent years, ECUs mounted on vehicles have proliferated, and their power consumption has increased in step with vehicle electrification and the rise of autonomous driving. In particular, applications such as advanced driver assistance systems (ADAS)[2], electric power steering (EPS)[3], and automatic braking require a redundant design with two identical circuits installed in a vehicle to improve safety, resulting in a trend towards a further increase in the number of capacitors used per ECU. However, the limited space available for installation in the vehicle body requires ECUs to process high currents in a compact size, which increases the amount of heat generated within the ECU. Therefore, capacitors are required to not only be more heat-resistant but also smaller in form factor while offering more capacitance than ever before.
Panasonic Industry began mass producing conductive polymer hybrid aluminum electrolytic capacitors in 2012, and has led the way with industry-first products. Recently, the company has further evolved its proprietary electrolyte and high-precision electrode foil winding technology with a view to commercial production of the ZL series capacitors. With a lineup of five major sizes, these capacitors overcome circuit design restrictions through heat control measures and achieve a one rank smaller size than the company's existing standard ZC series products without changing the capacitance.
Utilizing its proprietary device technology, Panasonic Industry will strive to contribute to enhancing the performance and reliability of electric vehicles and reduce equipment weight. This, in turn, will lead to improved fuel efficiency and contribute to decreased environmental impact by reducing the quantity of parts and materials used.
Panasonic's automotive conductive polymer hybrid aluminum electrolytic capacitors have the following features:
*1 As of February 28, 2024, the industry's highest capacitance models in five major sizes (ø5 x 5.8 to ø10 x 10.2) for automotive applications included in the conductive polymer hybrid aluminum capacitors are guaranteed to operate for 4,000 hours at 135°C (capacitors in sizes of ø5 and ø6 are guaranteed to operate for 2,000 hours at 135°C). (Panasonic Industry data)
*2 As of February 28, 2024, the industry's highest capacitance models in five major sizes (ø5 x 5.8 to ø10 x 10.2) for automotive applications included in the conductive polymer hybrid aluminum capacitors (Panasonic Industry data)
It is difficult to stabilize the characteristics of high-capacitance electrode foils in high-temperature environments, and there have been challenges in creating capacitors featuring both high capacitance and high heat resistance. Now, the Panasonic Industry has independently developed a new electrolyte that can stabilize electrode foil characteristics even in high-temperature environments by revising the material composition. By achieving a guaranteed operating temperature of 135°C, restrictions on circuit design due to thermal control measures can be overcome, even for high-capacitance type capacitors, leading to more compact ECUs.
To miniaturize a capacitor while maintaining its capacitance, it is necessary to increase the capacitance of its internal electrode foils. However, high-capacitance electrode foils have lower strength than general electrode foils, making them difficult to manufacture and ensure reliability. Panasonic Industry has succeeded in the stable mass production of high-capacitance electrode foils through its proprietary high-precision foil winding technology that maximizes winding dimensions and through the evolution of uniform polymer formation technology. Consequently, the ZL series capacitors in five major sizes have achieved the industry's highest level capacitance, which is more than 1.7 times that of the company's existing standard ZC series products. ZL series capacitors achieve the same performance in a smaller size compared to ZC series capacitors.
For the desired capacitance, the ZL series offers capacitors in a size one rank smaller than the Panasonic Industry’s existing standard ZC series products and achieves a reduction in the number of capacitors used. This saves space for capacitor mounting areas, contributing to a reduction in environmental impact through the miniaturization of equipment and a decrease in the number of parts and materials used.
Reduction of ripple current[4] and stabilization of voltage of DC/DC power supplies in ECUs, such as for ADAS, zone control units (ZCUs)[5], and engines
Reduction of ripple current in control system circuits of inverters for driving EPS, pumps, compressors, and motors
* Capacitors in sizes equal to or larger than ø6.3 can support vibration-resistant specifications (available sizes: ø6.3 x 6.1, ø6.3 x 8.0, ø8 x 10.5, ø10 x 10.5)
Abbreviation of Electronic Control Unit. General term for equipment (unit) that controls systems using electronic circuits, and mainly refers to units installed in vehicles.
ADAS is an abbreviation of Advanced Driver Assistance Systems.
ADAS is a general term for functions that assist driving by enabling the vehicle itself to grasp information about its surroundings, provide accurate displays and warnings to the driver, and control the vehicle on behalf of the driver, to ensure the safety and comfort of the driver.
EPS is an abbreviation of Electric Power Steering, which is a piece of equipment that electrically assists the steering of a vehicle. This piece of equipment drives the motor only when assistance is required. Compared to conventional hydraulic power steering (a system that uses engine power to drive the steering mechanism), it contributes to lower fuel consumption.
When a voltage fluctuation is applied to a capacitor, a charging or discharging current corresponding to the voltage fluctuation is applied to the capacitor. The current applied to this capacitor is referred to as a ripple current.
A ZCU refers to an architecture that employs a centralized gateway to manage communication and control applications installed in an electric vehicle. The applications are classified based on their implementation location (the vehicle is divided into two to six areas, such as the front or rear).
Devise Solutions Business Division, Panasonic Industry Co., Ltd.
https://industrial.panasonic.com/cuif/ww/contact-us?field_contact_group=2295&field_contact_lineup=1359
About Panasonic Industry Co., Ltd. Panasonic Industry Co., Ltd. was established on April 1, 2022 as an operating company in charge of the device business within the Panasonic Group in line with its shift to an operating company system. The mission of the company states that "We will open the way to a better future and continue to contribute to an affluent society through a variety of device technologies." On a global basis, the company has about 42,000 employees and achieved net sales of 1,149.9 billion yen for the fiscal year ended March 31, 2023. Against the backdrop of a labor shortage in manufacturing, the explosion of data with the rise of the information-based society, and greater demands for the environment and safety for the mobility society, the company will focus on areas where ongoing evolution is required and continue to provide customer value with distinctive features of unique material and process technologies such as capacitors, compact servomotors, EV relays, and electronic materials. Learn more about Panasonic Industry at https://www.panasonic.com/global/industry. |
The content in this website is accurate at the time of publication but may be subject to change without notice.
Please note therefore that these documents may not always contain the most up-to-date information.
Please note that German, French and Chinese versions are machine translations, so the quality and accuracy may vary.