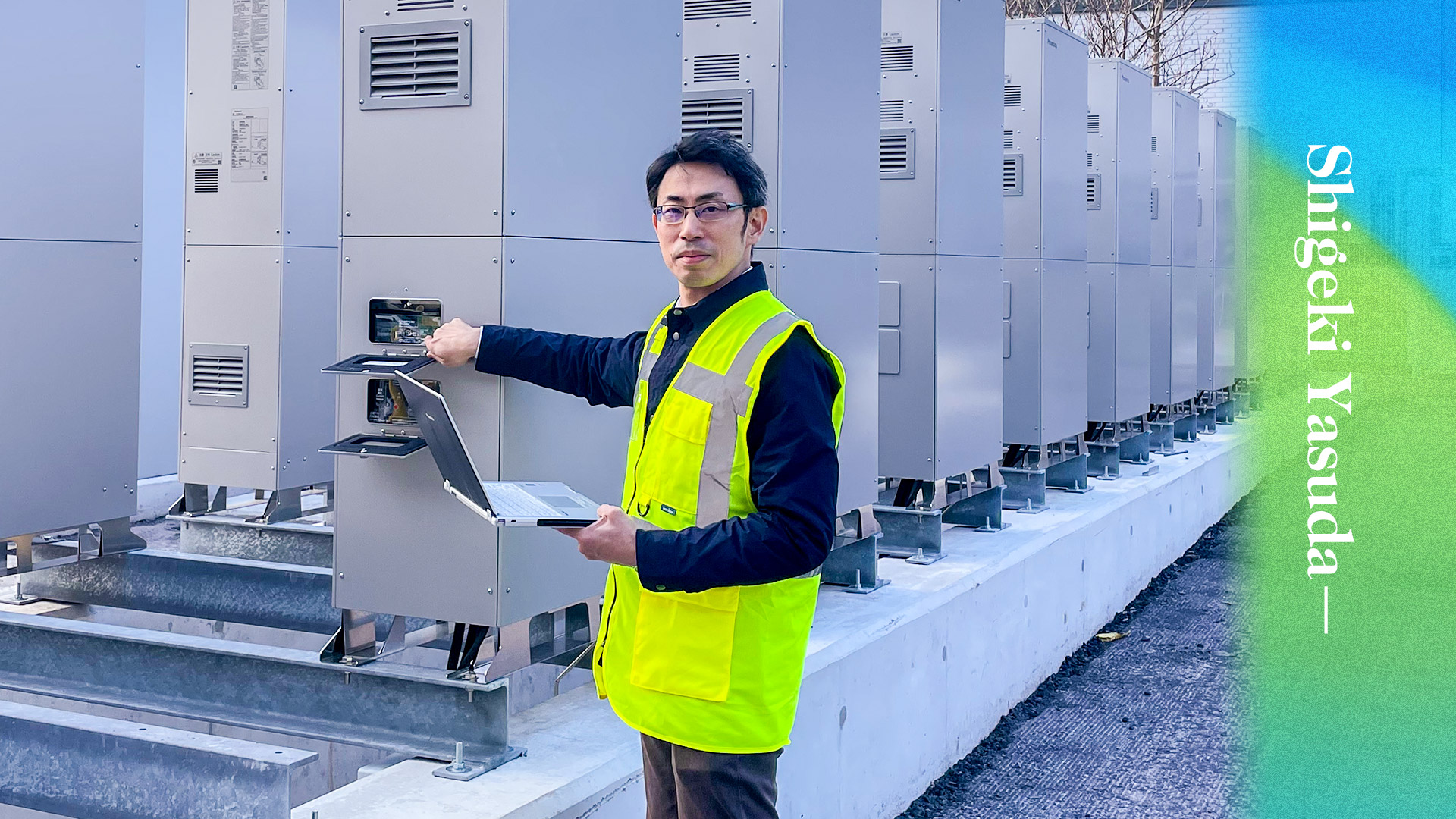
Feb 07, 2025
- Sustainability
- Feature Story
Panasonic Group People
Aiming for a Clean, Decarbonized Society with Panasonic HX: Shigeki Yasuda- Panasonic GREEN IMPACT
- Europe and CIS
The Panasonic Group’s long-term vision for reducing CO2 emissions and achieving a circular economy is known as “Panasonic GREEN IMPACT” (PGI). Through PGI, the Group is committed to developing its business by creating environmental value and realizing a carbon-neutral society.
In January 2023, Panasonic Housing Solutions Co., Ltd. (PHS) developed Sustainable Floor™, the first1 flooring material to use a base material (substrate) made from recycled wood and a coating derived from vegetable oils and fats (biomass). In addition, customers purchasing a Sustainable Floor™ also help contribute to forest conservation and the environment. Let’s take a look at how this unique product was developed.
Plywood is widely used for flooring, but the cost of this essential material continues to rise. PHS is keenly focused on promoting “Green Housing” and is committed to “realizing a lifestyle that benefits both people and the environment.” Determined to secure a stable supply of flooring materials that is both affordable and sustainable, the company introduced its Sustainable Floor product line.
“To ensure a stable supply of flooring materials, we’ve been developing recycled base materials made from chipboard since around 2017,” said Yusuke Yoshigai, Interior Material Product Planning and Development Department, Systems Business Division, PHS.
Chipboard, or “particle board,” is sheet wood made by mixing wood chips with an adhesive and then heating it in a mold (a process known as “thermoforming”). Typically used in furniture, chipboard is rarely used for flooring materials because it is weak to environmental factors, such as moisture.
“Our mission was to use chipboard to develop a full-scale, environmentally friendly flooring material. The project was greenlit at the end of March 2022, and with only around 10 months until launch, we had a daunting task ahead of us,” Yoshigai said.
Yusuke Yoshigai
“We immediately began prototyping, but overcoming chipboard’s weakness to moisture and intense pressure was more difficult than we’d anticipated. At one point, we thought we’d have to drastically change course to achieve our original vision.”
Then Yoshigai heard that a certain manufacturer was working with biomass coatings derived from vegetable oils and fats.
“We mainly handle products with ‘topcoat’ specifications, which means that a finishing coat can be applied on top of the decorative material. Because we create products that work well with coatings, we were convinced that we could revisit our product specifications and environmental story with this biomass coating as the crux.”
Workers measure the warping of flooring materials—verification testing like this helps prevent defects during installation.
Yoshigai and his team decided to use the manufacturer’s biomass topcoat for the finish on their Sustainable Floor™, with the intention of applying for Biomass Mark2 certification—which would be an industry first.
Sustainable Floor™ is coated with three layers to achieve the robustness, safety, and durability required for flooring materials.
Customers come into contact with the top layer on a daily basis, so PHS decided to use a scratch-resistant, durable, and proven conventional coating here while using the biomass coating for the bottom two layers.
“Being able to apply a coating derived from vegetable oils and fats rather than petroleum and obtain the Biomass Mark is a breakthrough for flooring product specifications,” said Yoshigai.
The development process wasn’t without its challenges. The biomass coating initially did not cure well and failed to meet PHS performance standards for flooring materials. Since the biomass coating was used for the bottom two layers, other issues included ensuring hardness, durability, and compatibility between the three layers.
“We made numerous prototypes in the lab and on the production line, constantly making improvements to achieve optimal performance in terms of curing and functionality,” said Yoshigai.
Development team checking the Sustainable Floor™ surface
For the substrate, PHS used its Sustainable Board, which is made from recycled construction waste and unused materials that would normally be discarded. By using waste as raw materials, Panasonic offers a path toward effective use of forest resources.
Sustainable Board is made from recycled materials, including construction waste.
“Since Sustainable Board is made from chips, we assumed that it could be recycled back into chips after use. However, during the development process, we discovered that reusing the material can be difficult.”
In the Sustainable Floor™ substrate, the front and back surfaces are covered with a moisture barrier to protect against moisture absorption and drying. The moisture barrier is difficult to recycle but is essential for ensuring quality and cannot be changed.
Said Yoshigai: “I was nearly at the end of my rope when I found a potential solution in Gunma Prefecture. For three years I had worked in Gunma, where the PHS flooring plant is located, and I wanted to see if there was anything we could do together with the local government, both to promote local production for local consumption and as a way of giving back to society.
“I discovered that Gunma was proactively creating forest conservation systems and partnering with the private sector. I immediately called the person in charge at the Gunma Prefectural Government and told him about our concept and what we hoped to achieve.”
Prefectural government officials were aware that Panasonic had several factories in Gunma but were unaware that they included a flooring factory. A single phone call led to Gunma Prefecture and PHS signing a “Partnership Agreement for Prefectural Forest Maintenance” for the maintenance and conservation of prefectural forests.
Yoshigai (second from left) in front of the Gunma Prefectural Government Building following the signing ceremony.
“This agreement has generated significant interest in PHS initiatives among the people of Gunma. Recently, we’ve been able to expand into new areas such as factory tours and joint participation in exhibitions,” said Yoshigai.
At the Wood Collection 2023 exhibition in Tokyo in February 2023, PHS exhibited Sustainable Floor™ at Gunma Prefecture’s booth, displaying a prototype made from Gunma Prefecture lumber.
Gunma Prefecture booth at Wood Collection 2023
Many of Japan’s forests are neglected, due in part to the high cost of maintenance and an aging corps of forestry workers. “The number of forest preserves in Japan is steadily rising, but simply having more forests isn’t enough; without proper management, these forests won’t prosper,” said Yoshigai. “When people think about protecting forests, they think about planting trees. But our agreement with Gunma Prefecture is for a system for properly managing forests—i.e., forest cultivation.”
The partnership agreement calls for PHS to work with Gunma Prefecture on the maintenance and conservation of prefecture-owned forests, improving their contribution to preventing global warming and other benefits.
Panasonic has introduced a system that allows customers to contribute to the environment when they purchase a Sustainable Floor™. For every 3.3 square meters they buy, a portion of the purchase price is allocated to forest conservation and maintenance activities for an area equivalent to the size of the palms of both hands (240 cm2). In addition, because the Sustainable Board substrate is made from recycled materials, every 3.3 square meters also stores approximately 38 kg of carbon (CO2 equivalent)3.
Said Yoshigai: “Purchasing a Sustainable Floor™ will help grow trees in the Gunma Tsumugi Forest. This tree-planting activity will support proper growth and cultivation of the forest. The name Gunma Tsumugi Forest also reflects our desire to continue to cultivate the relationship between people and forests.”
Sustainable Floor™ tree-planting activities help promote “Forest Conservation,” “Effective Use of Resources,” and “Reduced Fossil Fuels”—positive impacts friendly to people and the environment.
“We are considering expanding this system not only to flooring materials but also to other products. We believe that the Panasonic Group has a mission as a global company to deliver quality products to our customers and to support initiatives that help resolve environmental issues.”
Yoshigai visited Gunma Tsumugi Forest and hopes that “the relationship between people and forests will continue to grow.”
“In the process of launching Sustainable Floor™ we’ve received the help and cooperation of many people, both inside and outside Panasonic. Since it’s one of the few products in the industry with environmentally friendly features, it’ll be difficult to gain immediate acceptance by the market. However, I’d like to think that a decade from now, products like this will be mainstream. We hope that this development will be positioned as a pioneering step toward that outcome,” said Yoshigai.
1 As of January 2023 (based on PHS research)
2 The Biomass Mark certifies that products made from biological resources (biomass) conform to relevant laws, regulations, standards, and specifications for quality and safety.
3 Calculation is based on the Forestry Agency “Guidelines for Indication of Carbon Storage in Wood Used in Buildings” (Forestry Agency Director-General Notice No. 85, October 1, 2021).
The content in this website is accurate at the time of publication but may be subject to change without notice.
Please note therefore that these documents may not always contain the most up-to-date information.
Please note that German, French and Chinese versions are machine translations, so the quality and accuracy may vary.